Manufacturing Methods for a Solid Rocket Motor Propelling a Small, Fast Flight Vehicle
Author(s)
Mathesius, Kelly J.; Hansman, R. John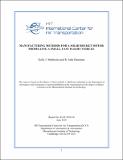
DownloadICAT-2019-10_Mathesius_Manufacturing_Methods_ICAT_Report.pdf (18.30Mb)
Metadata
Show full item recordAbstract
A gap exists in the design space for aircraft mass and speed: no flight vehicles with a mass of less than 10 kg and speed greater than 100 m/s are available. The small, fast "Firefly" flight vehicle is being developed to explore the capabilities and challenges for aircraft in this gap. The compact Firefly aircraft is configured around a long-endurance, end-burning solid rocket motor that provides 2-3 minutes of powered flight.
Challenges exist for manufacturing solid rocket motors for small, fast aircraft such as Firefly. Achieving desired motor performance requires a void-free propellant grain and thermal liner and a strong propellant-to-liner bond. However, observations and tests following several motor manufacturing attempts have revealed voids in the propellant and liner and delamination at the propellant-to-liner interface. Manufacturing defects such as these have led to large increases in chamber pressure and thrust during a static fire test of a motor.
This thesis describes the development and implementation of manufacturing methods for slow-burning, long endurance motors used in small, fast aircraft. Innovative tooling and rigorous procedures have been developed to help ensure the consistent production of a long-endurance solid rocket motor. Successful static firings of a test motor validate the effectiveness of many of the developed manufacturing methods.
Date issued
2019-06-05Series/Report no.
;ICAT-2019-10