An energy and environmental analysis of aerospace sheet metal part manufacturing
Author(s)
Rossie, Kathleen Eaton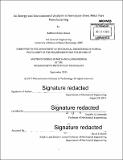
DownloadFull printable version (41.54Mb)
Other Contributors
Massachusetts Institute of Technology. Department of Mechanical Engineering.
Advisor
Timothy G. Gutowski.
Terms of use
Metadata
Show full item recordAbstract
In this thesis we analyze the energy and environmental impacts of sheet metal manufacturing, focusing on the aerospace industry. The motivation of this work is the introduction of a new incremental sheet forming (ISF) technology called RAFFT, which substitutes heavy part specific dies for flexible generic tools but with a slower processing rate. The analysis has two sections. The first section analyzes the current aerospace sheet forming technological and economic landscape in order to determine RAFFT's probable adoption rate and predict which technologies it will displace. The second section includes four energy and lifecycle analysis (LCA) case studies on traditional forming technologies. The first section maps the process capabilities of twenty sheet forming technologies. It also describes the business needs and typical practices of the aerospace industry, including a classification of the different business needs for parts. We find that stretch forming and flexforming (also known as a bladder press or hydroforming) dominate current aerospace production, and superplastic forming SPF is used when high formability is required. Machining is used extensively for very low volume production, such as prototyping. We find that the new RAFFT technology is best suited for very low volume production such as the production of replacement parts. The second section includes energy and LCA case studies for titanium SPF, aluminum SPF, flexforming, and stretch forming. Moreover, case studies on kirksite and cast iron die manufacturing are completed because these materials are used in forming dies. We find that SPF uses more energy and has higher impacts than stretch and flexforming. We also find that each technology has high "baseload" (no forming) electricity use due to heat losses in SPF and circulation of hydraulic fluid in stretch and flexforming, meaning that cycle time is a critical factor in electricity use. Lastly, we find that the material for the blank, the die, and the electricity can each dominate impacts depending on the particular characteristics of each case because a) the aerospace industry is willing to invest significant resources, be it time, energy, or material, to produce the desired part and b) the required amount of blank, die, and electricity are dependent on uncorrelated factors.
Description
Thesis: S.M., Massachusetts Institute of Technology, Department of Mechanical Engineering, 2015. Cataloged from PDF version of thesis. Includes bibliographical references (pages 223-246).
Date issued
2015Department
Massachusetts Institute of Technology. Department of Mechanical EngineeringPublisher
Massachusetts Institute of Technology
Keywords
Mechanical Engineering.