Materials and device design for MEMS piezoelectric mechanical vibration energy harvesters
Author(s)
Kim, Miso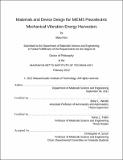
DownloadFull printable version (6.894Mb)
Alternative title
Materials and device design for microelectromechanical systems PVEHs
Other Contributors
Massachusetts Institute of Technology. Department of Materials Science and Engineering.
Advisor
Brian L. Wardle.
Terms of use
Metadata
Show full item recordAbstract
Piezoelectric vibration energy harvesters (PVEHs) for microelectromechanical systems (MEMS) have received considerable attention as an enabling technology for self-powered wireless sensor networks. MEMS-PVEHs are particularly attractive because of the potential to deliver power indefinitely and their ability to be integrated concurrently with microfabrication of sensor nodes. A key challenge has been insufficient power and voltage generation for practical applications. Along with research efforts on improved materials, efficient electronics, and fabrication of devices, modeling is an indispensable element in predicting and designing PVEHs. Here, an improved electromechanically-coupled model is developed including the ability to analyze proof mass effects and different electrode configurations. Although essential in microscale devices to move device resonances towards optimal frequency points for harvesting, proof masses have not been treated rigorously in extant work. An improved treatment of a rigid proof mass with rotation, and an exact treatment (two-beam model) of a flexible proof mass, are presented and experimentally verified using a macroscale, symmetric, bimorph, cantilevered PVEH device operating in {3-1} mode with a rigid proof mass, and a micron-scale Si cantilever with a flexible proof mass, respectively. Focused ion beam milling is used to create different flexible proof masses, and atomic force microscopy is used to study the mechanical behavior of micron-scale, single-crystal Si cantilevers. It is found that the two-beam model is necessary for the majority of the proof mass cases considered, especially when considering key power-generation characteristics such as strain developed in the piezoelectric layers. The effects of piezoelectric material properties on device performance are studied via model-based sensitivity analyses to gain insight into the design and selection of optimal piezoelectric materials for power and voltage generation. Notably, and non-intuitively, optimum power either at resonance or antiresonance is independent of the piezoelectric coupling constant of the piezoelectric material, obviating the oft-cited rationale for materials research to increase piezoelectric coupling coefficients. For example, in an exemplary PVEH optimization, maximum power and voltage are obtained at relatively low values (30-40% of bulk PZT, near AlN and ZnO film values) of piezoelectric coupling coefficients. The improved model is used as a multi-variable design tool for designing a novel piezoelectric/ultrananocrystalline diamond (UNCD) heterostructure MEMS-PVEH device. This thesis contributes to the development of MEMS- PVEHs by offering new insights at both the materials and system levels, including optimization findings using different objective functions, such as efficiency. Future work includes application of the modelderived piezoelectric materials design guidelines to aid in the design of optimal MEMS-PVEH systems, fabrication of designed UNCD/piezoelectric-based MEMS-PVEHs, and analytical and experimental studies of both structural and piezoelectric fatigue phenomena for enhanced reliability of PVEHs.
Description
Thesis: Ph. D., Massachusetts Institute of Technology, Department of Materials Science and Engineering, 2012. Cataloged from PDF version of thesis. Includes bibliographical references (pages 234-245).
Date issued
2012Department
Massachusetts Institute of Technology. Department of Materials Science and EngineeringPublisher
Massachusetts Institute of Technology
Keywords
Materials Science and Engineering.