Modeling, design, and optimization of permanent magnet synchronous machines
Author(s)
Angle, Matthew G. (Matthew Gates)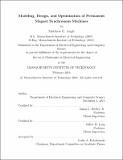
DownloadFull printable version (44.55Mb)
Other Contributors
Massachusetts Institute of Technology. Department of Electrical Engineering and Computer Science.
Advisor
James L. Kirtley, Jr. and Jerey H. Lang.
Terms of use
Metadata
Show full item recordAbstract
Improvement of performance of robots has necessitated technological advances in control algorithms, mechanical structures, and electric machines. Running, legged robots have presented challenges in the area of electric machinery in particular. In addition to the low-speed, high-torque, low-mass requirements on the machines, the act of running results in an unconventional drive cycle that consists of brief periods of high torque followed by long stretches of minimal torque requirement, a performance envelope that is not matched by commercially-available machines. An optimized motor would dissipate the minimum possible power over the given drive cycle, lowering temperatures and potentially reducing required battery mass or extending range. These performance requirements have motivated faster modeling techniques to enable optimization of designs for these unconventional applications. This thesis presents a novel, fast modeling method for permanent magnet synchronous machines consisting of a hybrid model comprising an explicit Maxwell solution and a Flux Tube solution. The Maxwell solution is performed for the rotor and airgap of the machine, where geometries are simple and materials are homogeneous. The stator, with its geometric complexities and non-linear materials, is modeled with a lumped-parameter model based on ux tubes. The two models are then stitched together, forced to be self-consistent with boundary conditions, and allowed to converge. This captures effects such as cogging torque as well as saturation of the core materials. The method is approximately four orders of magnitude faster than a reference finite element program (0.01 s versus 100 s) for the same accuracy. The modeling method is implemented for two topologies of surface-mount permanent-magnet machines, an internal-rotor machine and an external-rotor machine. It is then used to optimize machine design to a given drive cycle, including effects of core loss. A machine is built to demonstrate the validity of the model and optimization method and test results match predictions of instantaneous torque to within 5% at the worst point. Cogging torque is another aspect of performance that is important to machines for robotics and other applications. These pulsations in torque caused by magnet alignment with geometric features in the stator result in undesired vibrations and issues with control. One method, based on skew, for reducing or eliminating cogging torque is explored, and a simple analytical technique to predict the eect of skew is presented. Based on the machine optimized for the Cheetah, two additional machines were built to explore the effects of cogging: a skewed-rotor machine, and a skewed- stator machine. Each demonstrated reduction of a particular cogging harmonic or all of the cogging. The skewed machines reduced cogging by approximately 85%. Novel magnet shapes which further reduce cogging are presented and finite element modeling suggests that they can further reduce cogging by 60% over a straight skew. The design and optimization tools developed herein and described above were used to optimize a motor for the MIT Cheetah Robot. The resulting motor showed nearly an order of magnitude increase in torque density when compared to commercial, off-the-shelf machines (1.3 kg vs 820 g and 10 Nm vs 28 Nm) with simultaneous improvements to efficiency.
Description
Thesis: Ph. D., Massachusetts Institute of Technology, Department of Electrical Engineering and Computer Science, 2016. This electronic version was submitted by the student author. The certified thesis is available in the Institute Archives and Special Collections. Cataloged from student-submitted PDF version of thesis. Includes bibliographical references (pages 283-285).
Date issued
2016Department
Massachusetts Institute of Technology. Department of Electrical Engineering and Computer SciencePublisher
Massachusetts Institute of Technology
Keywords
Electrical Engineering and Computer Science.