Butterflies and batteries : advances in liquid repellent surfaces by anisotropic wetting and lubricant impregnation
Author(s)
Solomon, Brian R. (Brian Richmond)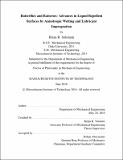
DownloadFull printable version (31.11Mb)
Alternative title
Advances in liquid repellent surfaces by anisotropic wetting and lubricant impregnation
Other Contributors
Massachusetts Institute of Technology. Department of Mechanical Engineering.
Advisor
Kripa K. Varanasi.
Terms of use
Metadata
Show full item recordAbstract
Recent advances in creating liquid-repellent surfaces have focused on decreasing the interaction between a liquid and a solid surface by modifying the surface's chemistry and cleverly designing its geometry on nano- and millimetric length scales. This thesis explores two advances to control a liquid's interaction with a surface: 1) deflectable structures that influence anisotropic wetting properties and 2) lubricant impregnated surfaces comprised of a porous surface and liquid lubricant. Through experimental characterization the mechanism by which deflectable scales on a butterfly wing cause anisotropic drop repellency is investigated. The design of lubricant impregnated surfaces is reviewed and expanded by demonstrating their potential for drag reduction and incorporation into electrochemical systems. The first part of this thesis characterizes how the unique structure of a butterfly's wings contributes to its anisotropic wetting properties. In particular, a water drop placed on the surface of a butterfly's wing will easily roll away from the butterfly's body, but will roll off at much higher angles toward the body. This phenomenon is observed and quantified using environmental electron microscopy and confocal microscopy. A theory that takes into account the deflection of the butterfly's scales explains the observed anisotropy and correlates with the observed roll-off on a wide range of butterfly species. Such deflectable surface structures offer a new way to tune the wetting properties of a surface. The second part of this thesis reviews and expands on lubricant impregnated surfaces. It explains how to achieve a stable lubricant impregnated surface and discusses its basic features including the wetting ridge and lubricant cloak. Motivated by the slippery nature of these surfaces, the potential of lubricant impregnated surfaces to reduce drag is detailed. A scaling model that incorporates the viscosity of the lubricant and elucidates the dependence of drag reduction on the ratio of the viscosity of the working fluid to that of the lubricant is presented. The model is validated by experiments conducted in a cone and plate rheometer where a drag reduction of 16% is measured. Finally, lubricant impregnated surfaces are applied to electrochemical systems. Measurements quantify how lubricant impregnated surfaces improve the flowability of a non- Newtonian lithium polysulfide flow electrode in which electronic conductivity is imparted by carbon particles. A framework for the design of such surfaces for a wide range of flow electrode solvents is used to incorporate lubricant impregnated surfaces into a Gravity Induced Flow Cell (GIFCell) prototype to enable the flow of highly conductive suspension.
Description
Thesis: Ph. D., Massachusetts Institute of Technology, Department of Mechanical Engineering, 2016. This electronic version was submitted by the student author. The certified thesis is available in the Institute Archives and Special Collections. Cataloged from student-submitted PDF version of thesis. Includes bibliographical references (pages 119-130).
Date issued
2016Department
Massachusetts Institute of Technology. Department of Mechanical EngineeringPublisher
Massachusetts Institute of Technology
Keywords
Mechanical Engineering.