Designing a microhydraulically-driven mini-robotic squid
Author(s)
Meng, Kevin Dehan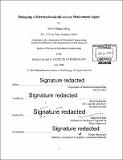
DownloadFull printable version (9.478Mb)
Other Contributors
Massachusetts Institute of Technology. Department of Mechanical Engineering.
Advisor
Sang-Gook Kim.
Terms of use
Metadata
Show full item recordAbstract
The realization of a standalone microrobotic platform has thus far been elusive due to size, weight, and power constraints. Recently, a novel microhydraulic electrowetting actuator (MEA) has been developed at MIT Lincoln Laboratory, enabling powerful, efficient, and scalable actuation. The MEA's use of efficient (17 > 65%), low-voltage electrowetting (<25 V) and high power density favorably positions the actuator for applications in microrobotics, which includes systems on the centimeter-scale and below. In this thesis, I present the design of a miniature robotic "squid" which features the MEA as the driving component. The system was inspired by cephalopod paralarvae, which predominantly rely on jet propulsion in their early stages of development. The squid robot can produce thrust by diaphragm pump-like operation, in either single-acting or double-acting modes. Since the actuator is a critical component, further modeling and analysis on the MEA is first presented and confirmed by experiments. After demonstrating actuator reliability, the design and fabrication of the squid are presented, from component-level considerations to system assembly procedures. High-resolution 3D printing methods are exploited to fabricate monolithic, multi-material structures and to develop passive flap check valves for gauging the pumping capability of MEA. The pump characteristics are modeled and tested, achieving flow rates of up to 1.79 mL/min. A finalized robotic squid design is predicted to swim at a velocity of 3 cm/s, which is comparable to that of young squid. Suggestions are made for the continued development of the mini-robotic squid. It is hoped that the squid design presented herein will serve as a precursor to more advanced, standalone microrobotic systems, which may find use in medicine and defense-related applications.
Description
Thesis: S.M., Massachusetts Institute of Technology, Department of Mechanical Engineering, 2016. Cataloged from PDF version of thesis. Includes bibliographical references (pages 90-93).
Date issued
2016Department
Massachusetts Institute of Technology. Department of Mechanical EngineeringPublisher
Massachusetts Institute of Technology
Keywords
Mechanical Engineering.