Predicting corrosion on protected buried steel natural gas distribution pipelines
Author(s)
Meyer, Lillian Ruth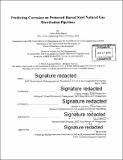
DownloadFull printable version (7.837Mb)
Other Contributors
Leaders for Global Operations Program.
Advisor
Georgia Perakis and Herbert H. Einstein.
Terms of use
Metadata
Show full item recordAbstract
PG&E uses cathodic protection, which connects the pipeline to sacrificial anodes that corrode instead of the pipeline, to prevent corrosion on its buried steel natural gas pipelines. However, corrosion leaks still occur. This thesis focuses on whether corrosion leaks can be predicted on steel distribution natural gas pipeline that is cathodically protected. By proactively understanding where leaks are most likely to occur rather than examining past leak performance, PG&E can better optimize its resources to reduce the risk of corrosion on its pipeline. We introduced logistic regression to model whether or not a corrosion leak will occur in a cathodic protection area, a one to ten mile length of pipe that uses the same corrosion control equipment. Two different types of data were available: data that are relatively static and data that are relatively dynamic with respect to time. We built two different sets of logistic regression models to examine two questions: (1) if data from one area can be used to predict where corrosion leaks will occur in another area; and (2) if data from one year can be used to predict where corrosion leaks will occur during the following year. The models for both questions use cross-validation to test the influence on model accuracy of the in-sample and out-of-sample data sets. The first model addresses the first question by using pipe characteristic and soil data with a mean average percentage error ranging from 35% to 96%. The significant factors in a given cathodic protection area (CPA) that consistently drive the model include: length of steel main pipe; percent of steel main pipe designated as low pressure; the average moist bulk density of the soil; the variation of soil pH; average clay content in the soil; variation of clay content in the soil; and the average saturated hydraulic conductivity of the soil. The second model addresses the second question by using the previous year's routine maintenance and weather data with a mean average percentage error ranging from 40% to 81%. The significant factors in a given CPA that consistently drive the model include: the length of steel main pipe and average temperature.
Description
Thesis: S.M., Massachusetts Institute of Technology, Department of Civil and Environmental Engineering, 2016. In conjunction with the Leaders for Global Operations Program at MIT. Thesis: M.B.A., Massachusetts Institute of Technology, Sloan School of Management, 2015. In conjunction with the Leaders for Global Operations Program at MIT. Cataloged from PDF version of thesis. Includes bibliographical references (pages 59-60).
Date issued
2015Department
Leaders for Global Operations Program at MIT; Massachusetts Institute of Technology. Department of Civil and Environmental Engineering; Sloan School of ManagementPublisher
Massachusetts Institute of Technology
Keywords
Civil and Environmental Engineering., Sloan School of Management., Leaders for Global Operations Program.