The identification and validation of case hardening for extending charcoal briquette extruder lifespan
Author(s)
Wang, Lindsey (Lindsey M.)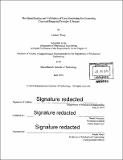
DownloadFull printable version (7.371Mb)
Other Contributors
Massachusetts Institute of Technology. Department of Mechanical Engineering.
Advisor
Daniel Sweeney.
Terms of use
Metadata
Show full item recordAbstract
Appropriate Energy Saving Technologies Ltd. (AEST) located in Soroti, Uganda aims to reduce deforestation and indoor air pollution through their sustainable charcoal briquettes. However, the charcoal mixture causes extreme wear in the briquette extruding machines, restricting the business's ability to scale up. Case hardening was identified as a potential solution to increase the wear resistance of the extruders by diffusing carbon into key components of the machine such as the screw. Several steps were taken at MIT D-Lab to validate the case hardening strategy including measuring the carbon content of steel samples from AEST's machines; designing a furnace from materials widely available in Soroti that could achieve the temperature necessary for case hardening; and evaluating different types of quenching liquids. Once the process had been validated, D-Lab researchers and AEST employees implemented the procedure at AEST's briquette production site, building a brick furnace and case hardening three screws. AEST has since reported that the case hardened screw produces twice as many briquettes during its lifespan as the untreated screw does. AEST is now looking to case harden other machines at their workshop to increase overall briquette output.
Description
Thesis: S.B., Massachusetts Institute of Technology, Department of Mechanical Engineering, 2016. Cataloged from PDF version of thesis. Includes bibliographical references (page 43).
Date issued
2016Department
Massachusetts Institute of Technology. Department of Mechanical EngineeringPublisher
Massachusetts Institute of Technology
Keywords
Mechanical Engineering.