Reducing reagent waste through process improvement and preventive maintenance
Author(s)
Gobel, Amy Rose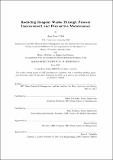
DownloadFull printable version (4.694Mb)
Other Contributors
Leaders for Global Operations Program.
Advisor
Nikos Trichakis and Dan Whitney.
Terms of use
Metadata
Show full item recordAbstract
Quest Diagnostics has committed to reducing operating expenses by $1.3B between 2012 and 2017. A portion of the cost-saving initiative focuses on reagents - expensive liquids that are combined with patient samples to detect compounds of interest. This project aims to reduce reagent waste for high-volume diagnostic tests run on an instrument platform that generates a relatively high amount of reagent waste. Waste, in this context, means any reagent that does not generate unique patient results. Therefore critical components of the quality system, such as quality control and calibration tests, are designated waste even though they are a necessary expenditure. Quality control (QC) samples and mechanical errors accounted for 5.2% and 4.4%, respectively, of all reagent usage prior to the start of the project. Mechanical errors occur when the diagnostic testing platform encounters something unexpected, such as debris or a reading that indicates insufficient sample volume, which interrupts sample processing. The instrument jettisons this test and attempts to repeat the assay. Initial discussions with laboratory representatives revealed differing interpretations of quality control requirements. All sites using the platform of interest were then surveyed to gauge the extent of variation. All sites met quality control requirements but several exceeded them. The most pertinent variations are listed below. 1. Frequency: Several sites ran control samples more often than established in Standard Operating Procedure (SOP) requirements, increasing total QC usage by over 70%. 2. Container size: The choice of container determines the amount of "dead volume", material that the instrument cannot access and must be discarded. Some sites used containers with 12.8 times the dead volume required in the smallest option. 3. Reuse policy: Some labs reuse containers of quality control materials across multiple batches. Reusing QC material further reduces the amount of dead volume discarded, but using new QC materials eliminates the possibility of evaporation between batches. An interdisciplinary team of experts tasked with maintaining the SOPs has reviewed these results and will clarify the appropriate SOP interpretation to unify practices across laboratories. In order to understand mechanical errors, I observed routine maintenance at four sites and found that business units did not consistently share best practices. Collaborating with vendor representatives and operators, I launched an Autonomous Maintenance (AM) pilot program in order to develop training materials capturing institutional knowledge and to test additional maintenance procedures. The AM activities generated 29 training documents, which were added to a national database of competency training materials. All operators certified to operate the testing platform will be required to review and pass comprehension quizzes on the training materials. As the Marlborough site continues to develop improvements to the maintenance procedures, these changes will be shared with the vendor and incorporated into training documents.
Description
Thesis: M.B.A., Massachusetts Institute of Technology, Sloan School of Management, in conjunction with the Leaders for Global Operations Program at MIT, 2017. Thesis: S.M. in Engineering Systems, Massachusetts Institute of Technology, School of Engineering, Institute for Data, Systems, and Society, in conjunction with the Leaders for Global Operations Program at MIT, 2017. This electronic version was submitted by the student author. The certified thesis is available in the Institute Archives and Special Collections. Cataloged from student-submitted PDF version of thesis. Includes bibliographical references (page 91).
Date issued
2017Department
Leaders for Global Operations Program at MIT; Massachusetts Institute of Technology. Engineering Systems Division; Massachusetts Institute of Technology. Institute for Data, Systems, and Society; Sloan School of ManagementPublisher
Massachusetts Institute of Technology
Keywords
Sloan School of Management., Institute for Data, Systems, and Society., Engineering Systems Division., Leaders for Global Operations Program.