Modeling of two-body fatigue wear of cylinder liner in internal combustion engines during the break-in period and its impact on engine lubrication
Author(s)
Gu, Chongjie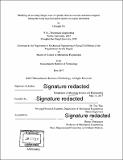
DownloadFull printable version (18.09Mb)
Other Contributors
Massachusetts Institute of Technology. Department of Mechanical Engineering.
Advisor
Tian Tian.
Terms of use
Metadata
Show full item recordAbstract
Internal combustion engines are widely utilized in modem automobiles. Around 10% of the total fuel energy is dissipated to heat due to mechanical friction, among which 20% is caused by the contact between the cylinder liner and the piston rings. The wear of cylinder liner not only leads to surface damage, but also results in the change of liner lubrication conditions. Therefore, a large number of tests are performed by researchers to investigate the liner wear process and its impact on engine lubrication. This work is the first step toward developing a wear model to predict the evolution of liner roughness and ring pack lubrication during break-in period. A physics-based liner wear model is built in this work, with focus on two mechanisms: surface plastic flattening and fatigue wear. Both mechanisms are simulated through a set of governing equations and are coupled together to complete the algorithm of the liner wear model. Simulations of break-in wear are performed to different liner surfaces finishes, with different external normal pressures. Simulation results indicate that the liner wear rate depends on the size and shape of liner surface asperities, which may provide guidance for surface manufacturing. The results also show consistence with the Archard's wear law, describing the proportional correlation between normal pressure and steady state wear rate. This wear model is then used to study the influence of liner wear on engine lubrication. Through the friction for entire engine cycles, simulated results are compared with experimental friction measurements. The comparison shows that the calculated friction evolution during break-in has the same trend and comparable magnitude as the measurements, indicating the efficiency of the wear model. Some initial work of modeling of third-body abrasive wear is also discussed in this thesis.
Description
Thesis: S.M., Massachusetts Institute of Technology, Department of Mechanical Engineering, 2017. Cataloged from PDF version of thesis. Includes bibliographical references (pages 104-108).
Date issued
2017Department
Massachusetts Institute of Technology. Department of Mechanical EngineeringPublisher
Massachusetts Institute of Technology
Keywords
Mechanical Engineering.