Design and manufacturing of a benchtop thermoforming machine
Author(s)
Owusu-Akyaw, Akwasi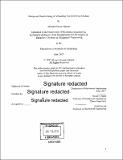
DownloadFull printable version (6.800Mb)
Other Contributors
Massachusetts Institute of Technology. Department of Mechanical Engineering.
Advisor
David E. Hardt.
Terms of use
Metadata
Show full item recordAbstract
The following work details the design and fabrication of a tabletop thermoform machine with the goal of making this machine cheaper than the ones on the market, yet able to fulfill specific requirements. These functional requirements include creating parts that have dimensions within .05" of the original part; thermoforming plastics that range between a 3" x 3" and 12" x 12" size; and having the ability to heat the plastic to at least 150°C in order to thermoform plastics such as polycarbonate. In addition, this machine had to be simple to manufacture and use. In order to achieve these requirements, a top to bottom drape forming architecture with a four bar linear slider and carriage, was constructed. In order to constrain the plastics of different sizes, two similar, modular wooden plates were used such that the plastic was held in between them via t-nuts and screws. When the user clamps the plastic onto the carriage, he or she slides the carriage upwards to an oven that radiates heat via nichrome wire on a mica sheet. Once the desired temperature is reached, the user then slides the carriage down onto a vacuum box platform, where a mold is present, and forms the plastic over the mold. While that happens, a negative pressure is applied inside the box via a standard commercial vacuum, so that the plastic adheres more closely to the mold. For the testing process, this work focuses on two manufacturing strategies for thermoforming parts: heating the air to the glass transition temperature before thermoforming, and heating the plastic to the glass transition temperature before thermoforming. Once this test was performed, the dimension of each plastic part was examined in order to see if the tolerance levels were reached. In addition, this test determined whether or not there was a statistical significance between the qualities of parts made by either of these processes. In the end, the thermoform machine was only able to reach an average tolerance of .07" for the created parts. In addition, there was no statistical significance between the part qualities of either one of the tested manufacturing processes. Some of the main reasons behind this include having an ineffective vacuum box and clamp design issues, which will be focused on in the future iteration of this project.
Description
Thesis: S.B., Massachusetts Institute of Technology, Department of Mechanical Engineering, 2017. Page 39 blank. Cataloged from PDF version of thesis. Includes bibliographical references (page 38).
Date issued
2017Department
Massachusetts Institute of Technology. Department of Mechanical EngineeringPublisher
Massachusetts Institute of Technology
Keywords
Mechanical Engineering.