Next generation probabilistic prediction model for submarine propulsion shaft life
Author(s)
Huynh, Daniel Duc Cong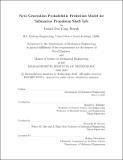
DownloadFull printable version (11.59Mb)
Other Contributors
Massachusetts Institute of Technology. Department of Mechanical Engineering.
Advisor
Ronald G. Ballinger and Alexander H. Slocum.
Terms of use
Metadata
Show full item recordAbstract
With the development of the U.S. Navy's new COLUMBIA class ballistic missile submarine, the Navy plans to implement a new, longer operational inspection interval for the propulsion shaft system, attempting to double the current 6-year inspection interval for the OHIO class of submarine it is replacing. However, an initial study conducted suggests unsatisfactory levels of failure at this interval due to corrosion fatigue, although with a high level of uncertainty. This thesis addresses that uncertainty by developing a more robust probabilistic model for submarine propulsion shaft reliability in order to more accurately predict probabilities of failure. To improve upon previous efforts, all the components and failure modes of the propulsion shaft were first identified. While the most likely scenario involves water ingress and a wetted propulsion shaft leading to corrosion, pitting, and cracking, other factors that could contribute to shaft failure include damage during installation or failure of cathodic protection systems. Using literature and data gathered during visits to Portsmouth Naval Shipyard (PNSY), these failure modes were approximated with appropriate relationships and statistical distributions and ultimately combined to form a complete probabilistic model of the propulsion shaft system, including all the expected components and the best physics available. Additionally, while this model was designed with extension to the COLUMBIA class of submarine in mind, it can be tailored and easily modified to apply to a broad range of shafting systems, including other classes of submarines, conventional surface ships, and even offshore platforms. The GoldSim program was used as the vehicle for the model, with failure probabilities for the submarine shaft predicted using Monte Carlo simulations. To calibrate the model, outputs from the probabilistic model were compared against hypothetical shaft inspection data, adjusting distributions and variables as appropriate to match target values. While the model used the OHIO class submarine as its baseline, it is expected that the new COLUMBIA class shafting system will use similar materials and have a similar configuration. These inspections have typically taken place at around the 6-year operational interval, but the calibrated model can be used to predict propulsion shaft failures at a range of inspection intervals.
Description
Thesis: Nav. E., Massachusetts Institute of Technology, Department of Mechanical Engineering, 2018. Thesis: S.M., Massachusetts Institute of Technology, Department of Mechanical Engineering, 2018. This electronic version was submitted by the student author. The certified thesis is available in the Institute Archives and Special Collections. Cataloged from student-submitted PDF version of thesis. Includes bibliographical references (pages 81-85).
Date issued
2018Department
Massachusetts Institute of Technology. Department of Mechanical EngineeringPublisher
Massachusetts Institute of Technology
Keywords
Mechanical Engineering.