Microjet impingement cooling of high power-density electronics
Author(s)
Walsh, Stephen Michael, Ensign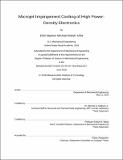
DownloadFull printable version (7.261Mb)
Other Contributors
Massachusetts Institute of Technology. Department of Mechanical Engineering.
Advisor
Bernard A. Malouin Jr. and Evelyn N. Wang.
Terms of use
Metadata
Show full item recordAbstract
The increasing power density of advanced electronics, and in particular Gallium Nitride (GaN) high electron mobility transistors (HEMTs) in RF power amplifiers, represents a major challenge in thermal management. Reducing the operating temperature, by means of effective cooling, improves both the performance and lifetime of the device. In this work, the high heat transfer capability of microjet impingement was leveraged to bring cooling directly to the backside of the electronic device. Previous experimental studies characterized the effects of geometrical factors, such as diameter, pitch, and standoff, on heat transfer performance. Insights from these studies were used to design a square array of sixteen 100 μm jets and a circular array of nineteen 116 μm jets. These designs were then built using standard silicon micro-fabrication techniques and bonded to an integrated heater, which matched the heat generation profile of a HEMT device. A fully conjugate numerical model of the fluid dynamics and heat transfer in COMSOL Multiphysics allowed for visualization of the fluid flow within the assembly. The model was used to predict heat transfer coefficients of over 250 kW/m²-K, showing strong agreement with correlations in the microjet literature. Integration of the microjet device into a closed flow loop demonstrated modest total flow rates and pressure drops. The microjet performance was then characterized using a free space micro-Raman thermography system with spatial resolution of 1 μm. For the first time, two-dimensional scans of a device under power were taken with jet impingement cooling on the backside. The micro-Raman thermography measurements confirmed heat transfer coefficients of 250 kW/m²-K on a device with a heat flux of 5500 W/cm² and a temperature rise of 46 ± 2 °C. In this thesis, practical concerns including microjet orifice clogging and backside erosion were answered through completion of a 1000-hour extended lifetime test. This thesis provides both numerical and experimental research demonstrating the impact of microjet impingement cooling and high spatial resolution micro-Raman thermography.
Description
Thesis: S.M., Massachusetts Institute of Technology, Department of Mechanical Engineering, 2018. This electronic version was submitted by the student author. The certified thesis is available in the Institute Archives and Special Collections. Cataloged student-submitted from PDF version of thesis. Includes bibliographical references (pages 86-90).
Date issued
2018Department
Massachusetts Institute of Technology. Department of Mechanical EngineeringPublisher
Massachusetts Institute of Technology
Keywords
Mechanical Engineering.