Combined tensile-compressive biaxial loading of Li-ion battery components
Author(s)
Byrd, Nathaniel J. (Nathaniel Joseph)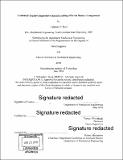
DownloadFull printable version (16.58Mb)
Other Contributors
Massachusetts Institute of Technology. Department of Mechanical Engineering.
Advisor
Tomasz Wierzbicki.
Terms of use
Metadata
Show full item recordAbstract
Lithium-ion batteries under a mechanical load can develop failures in the internal multi-layer structure. Due to the flammable materials required for construction, the safety of the battery has been in question since it was first developed. Internal failures can create a short circuit which may lead to thermal runaway, resulting in fire and sometimes the explosion of the battery. Due to the increasing use of lithium-ion batteries in military and consumer products, the number of incidents involving batteries has also risen and with it a growing concern for safety. The larger batteries required for unmanned vehicles and electric vehicles increase the potential for damage due to a battery fire aboard a ship or a battery damaged in a collision. This thesis investigates the failure mechanism of internal lithium-ion battery components when subject to a constant out-of-plane compression while applying and increasing a decoupled in-plane tension until failure. This thesis also describes the methods used to optimize the mechanical system designed to apply constant compression while increasing tension. The results will be used to characterize and anticipate the effect of lateral compression on the failure load of lithium-ion battery cells. The existing microstructural based finite element model can be modified to the experimental conditions in this thesis in order to compare the experimental and modeled results. This comparison will be used to refine and validate the micro model and ultimately bring us closer to improving the design of lithium-ion batteries. Experimental results showed there is a quantifiable relationship between the amount of pre-compression internal battery components are exposed to and the maximum failure load. In the tested 0 to 30 MPa compression range was a 40% reduction in fracture displacement and a 20% reduction in load displacement. The change in failure order, predicted by the micro model was validated by this experimental data. However, failure did not occur in the area of compression which indicates friction due to the compression had a significant effect on testing therefore a design to eliminate friction was proposed.
Description
Thesis: Nav. E., Massachusetts Institute of Technology, Department of Mechanical Engineering, 2018. Thesis: S.M., Massachusetts Institute of Technology, Department of Mechanical Engineering, 2018. Cataloged from PDF version of thesis. Includes bibliographical references (pages 62-63).
Date issued
2018Department
Massachusetts Institute of Technology. Department of Mechanical EngineeringPublisher
Massachusetts Institute of Technology
Keywords
Mechanical Engineering.