Aerospace composite manufacturing cost models as geometric programs
Author(s)
Nill, Scott T. (Scott Thomas)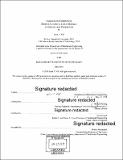
DownloadFull printable version (15.81Mb)
Other Contributors
Massachusetts Institute of Technology. Department of Mechanical Engineering.
Advisor
Warren Hoburg.
Terms of use
Metadata
Show full item recordAbstract
The introduction of large, composite transport aircraft, such as the Airbus A350 and the Boeing 787, has been fraught with billions of dollars of production cost overruns. This research develops a novel approach to manufacturing cost modeling during the conceptual design phase using Geometric Programming (GP). A new formulation of a closed queuing network as a GP is presented to capture the crucial cost trade-offs between capacity and inventory. Additionally, GP models are presented for modeling unit processes in composite manufacturing and for modeling cost accounting metrics. Applied to the challenges of conceptual design for composite aircraft, the cost models can be used as a tool to help inform decisions about which manufacturing process to use and what type of supply chain should be deployed. The special sensitivity-analysis properties of the GP solutions can be exploited to explain how different aspects of the design drive manufacturing costs and to find highly sensitive areas of the trade-space that would have a large impact on cost if the design needed to be altered. The framework is demonstrated for fast but informative analyses of process trade-offs in composite fuselage fabrication.
Description
Thesis: Ph. D., Massachusetts Institute of Technology, Department of Mechanical Engineering, 2018. Cataloged from PDF version of thesis. Includes bibliographical references (pages 108-110).
Date issued
2018Department
Massachusetts Institute of Technology. Department of Mechanical EngineeringPublisher
Massachusetts Institute of Technology
Keywords
Mechanical Engineering.