Modeling the effects of liner pores on piston ring lubrication in internal combustion engines
Author(s)
Sacherer, Jérôme.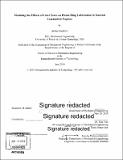
Download1119389149-MIT.pdf (11.74Mb)
Other Contributors
Massachusetts Institute of Technology. Department of Mechanical Engineering.
Advisor
Tian Tian.
Terms of use
Metadata
Show full item recordAbstract
Automotive manufacturers are increasingly replacing traditional cast iron liners in the internal combustion engines of commercial vehicles with spray-coated liners. While not the original intention, these new, porous liners are suspected to reduce hydrodynamic friction. The interaction of pores with piston ring and liner lubrication is studied in this work. Preliminary computational fluid dynamics simulations are performed on a single, idealized pore geometry, including surface tension but no cavitation due to computational cost limitations. Potential mechanisms for displacement of oil out of the pore are investigated, as this would improve subsequent ring lubrication. Pressure-driven flow is found to dominate this process, though surface tension also has an impact: it can trap air bubbles in the pore and level out accumulated oil back into the evacuated pore. A deterministic model exists to predict hydrodynamic pressure and friction for rough and honed liner surfaces. This model, however, assumes fully flooded boundary conditions. A modification to the governing equation for the regions beyond the full film boundaries is developed by introducing a diffusive velocity profile. The diffusion provides a transition between an oil film on the liner experiencing uniform flow to full film Couette flow. This change enables the large pore geometry to be accommodated by the model without unrealistic premature film attachment all the while maintaining the continuous transition between full film and cavitation. Results from the model indicate that the pore can act as an oil supply, extending the wetting region beneath the ring and consequently allowing for greater pressure generation and larger, desirable load carrying capacity. Cavitation also plays a critical role in the pore interaction; early cavitation in the pore can split the full film region, significantly compromising the load carrying capacity. Cavitation is also found to potentially make use of the pore's oil supply to redistribute oil onto the liner. In general, the pore causes a substantial drop in lift force, increasing the coefficient of friction as a result, though in some cases an extended wetting region can counter this effect.
Description
Thesis: S.M., Massachusetts Institute of Technology, Department of Mechanical Engineering, 2019 Cataloged from PDF version of thesis. Includes bibliographical references (pages 71-72).
Date issued
2019Department
Massachusetts Institute of Technology. Department of Mechanical EngineeringPublisher
Massachusetts Institute of Technology
Keywords
Mechanical Engineering.