Simulation-guided lattice geometry optimization of a lightweight metal marine propeller for additive manufacturing
Author(s)
Dagres, Ioannis.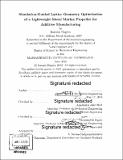
Download1117714356-MIT.pdf (15.93Mb)
Other Contributors
Massachusetts Institute of Technology. Department of Mechanical Engineering.
Advisor
Anastasios John Hart and Themistoklis Sapsis.
Terms of use
Metadata
Show full item recordAbstract
Additive manufacturing (AM) is one of the most promising emerging technologies for advanced mechanical systems. When compared to conventional manufacturing processes, AM offers major advantages in production of complex components, enhanced performance, material savings, and supply chain management. These advantages are driving a shift towards AM in marine industry, which is highlighted by recent relative publications of the American Bureau of Shipping (ABS) and others. This thesis focuses on the design of an exemplary marine propeller that leverages the advantages of AM through simulation-guided design of an internal lattice structure. Specifically, a B-series Wageningen three-blade propeller model, provided by Naval Warfare Surface Center (NSWC) Carderock, was used as a baseline. Its open water loading conditions were calculated numerically using OpenFOAM®, a computational fluid dynamics (CFD) software. The CFD results were verified using the provided test data, the thrust and torque coefficients differed by a maximum of 2.7%. The derived loads were introduced to the Finite Element Analysis (FEA) based optimization utility in Autodesk® Netfabb Ultimate, in order to identify the optimum lattice geometry for this application. The design limitations were dictated by the material (316SL stainless steel), the metal additive manufacturing process, and the propeller outer geometry.A variety of lattice infill designs were generated to create a design trade space and conclude to the most appropriate design for this application. The design with the best performance was a hexagonal grid lattice with 1 mm wall thickness, which was prescribed as a manufacturing constraint (i.e., the thinnest wall). The material volume was reduced by more than 50%, while exhibiting a satisfactory safety factor based on the material properties and the simulated loads. Sections of the propeller were prototyped by Desktop Metal Studio System[superscript TM].
Description
Thesis: Nav. E., Massachusetts Institute of Technology, Department of Mechanical Engineering, 2019 Thesis: S.M., Massachusetts Institute of Technology, Department of Mechanical Engineering, 2019 Cataloged from PDF version of thesis. Includes bibliographical references (pages 149-153).
Date issued
2019Department
Massachusetts Institute of Technology. Department of Mechanical EngineeringPublisher
Massachusetts Institute of Technology
Keywords
Mechanical Engineering.