Manufacture of aerospace-grade thermoset and thermoplastic composites via nanoengineered thermal processing
Author(s)
Daso, Frederick O.(Frederick Odien)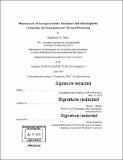
Download1119730090-MIT.pdf (19.49Mb)
Other Contributors
Massachusetts Institute of Technology. Department of Aeronautics and Astronautics.
Advisor
Brian L. Wardle.
Terms of use
Metadata
Show full item recordAbstract
Aerospace manufacturers continue to rely on composite materials to make aerovehicles lighter and stronger, particularly employing carbon fiber reinforced plastics (CFRP) using carbon microfiber reinforcement with thermoset and thermoplastic polymer matrices. With the increasing use of such composites, the need for energy-efficient, cost-effective methods to produce composite structures is desired. Traditional curing processes such as autoclaves and ovens rely on convective heat transfer, which has fundamental inefficiencies and several limitations including infrastructure cost and throughput bottlenecks. Similarly, hot presses (usually for thermoplastic matrices) for processing composites through conductive heat transfer are limited to a narrow range of part geometries. Direct Joule heating with carbon nanotube (CNT) film network heaters has shown significant promise to overcome these key manufacturing challenges of composites in the aerospace industry. This Out-of-Oven (000) conductive curing technique has been shown to cure aerospace-grade out-of-autoclave (OoA) CFRP prepreg laminates with equivalent quality to that achieved with the manufacturer's recommend cure cycle (MRCC) in an oven. Herein are introduced three new advances utilizing OoO heating: i) the first application of OoO heating to processing aerospace-grade thermoplastic (polyetheretherketone, PEEK) CFRP prepreg, ii) a new method to accelerate the cure cycle of OoA CFRP prepreg, and iii) a novel strategy towards eliminating cure-driven deformations within composites with curved geometries via spatially-tailored OoO 'zonal curing'. OoO is found to produce PEEK CFRP plate specimens comparable or better than MRCC autoclave and hot press-produced laminates, both in terms of quality and strength, with advantages in spatial and temporal control noted. Cure cycle duration for the thermoset OoA CFRP can be shortened by more than 60% while still producing flat laminates with similar quality and (short beam shear, SBS) strength compared to MRCC-produced specimens. The OoO zonal curing is shown via modeling to reduce the cure-driven deformation in thermoset OoA CFRP L-shape cuved parts by at least 11%. By demonstrating OoO curing's several advantages due to the CNT film's ability to maintain thermal stability at high temperatures, the near-instantaneous temporal control, the results in this work show that OoO curing can contribute to the next leap in composites manufacturing capability and technology. While the work herein has focused on aerospace-grade CFRP materials with the highest performance and quality, OoO is applicable to other materials in other industries including wind, ground vehicle, and infrastructure applications of a variety of advanced composites, including glass fiber reinforced plastics (GFRP).
Description
Thesis: S.M., Massachusetts Institute of Technology, Department of Aeronautics and Astronautics, 2019 Cataloged from PDF version of thesis. Includes bibliographical references (pages 138-149).
Date issued
2019Department
Massachusetts Institute of Technology. Department of Aeronautics and AstronauticsPublisher
Massachusetts Institute of Technology
Keywords
Aeronautics and Astronautics.