Electricity sensors for resource efficiency and supply chain visibility in factories
Author(s)
Talampas, Joseph P.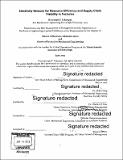
Download1119537784-MIT.pdf (10.58Mb)
Other Contributors
Sloan School of Management.
Massachusetts Institute of Technology. Department of Mechanical Engineering.
Leaders for Global Operations Program.
Advisor
Maria Yang and Charles H. Fine.
Terms of use
Metadata
Show full item recordAbstract
Cost pressures on factories and the growing movement towards sustainability are key motivations behind Li & Fung's (LF) drive towards innovation. Supply chain digitalization through initiatives such as the Internet of Things (IoT) and big data is one of LF's pillars in its Three Year Plan. LF is committed to making data visible, digitally connecting, and understanding and improving resource efficiency in its supply chain. However, there is an immense amount of data across LF's -16,000 partner factories that remains largely invisible and untapped to fulfill these objectives. This thesis serves as a case study that explored the use of sensors to monitor electricity consumption in factories. Prior to this thesis, small-scale pilots in China and India yielded energy saving opportunities of up to 15% of a factory's consumption, in a payback period of 1-2 years. Given these, a factory-wide sensor installation was developed and tested in one partner factory. A six-step framework, and tools to support the initiative, were also developed and tested. Elements of this framework include: i) a method for prioritizing factories for rolling-out the sensor installation, 2) capacity-building materials enabling factories to install sensors and derive insights from the data, 3) environmental metrics for Li & Fung to benchmark factories, and 4) financing or incentive scheme to encourage factory participation. The case study in a factory in Dongguan, China yielded 45% energy savings in the air compressor, a payback period of three months, and additional savings opportunities from improving the use of CNC and injection molding machines. Although the sensors identified energy savings, feedback from the case study and from vendor road shows reveals that using sensors may be attractive to some, but not all factories, due to upfront cost, sensitivity to data, or competing investments or initiatives to reduce costs and/or improve sustainability. LF may consider relying the Higg Index to improve visibility into the resource efficiency and sustainability of its network, and to segment the market for the electricity sensors project. Using the Higg Index can also provide insight to appropriate measures that a factory can take, ranging not only from installing electricity sensors but also with energy audits or direct investments in energy-efficient equipment. Sensors can also be part of a portfolio of digital, operations, and sustainability initiatives to develop a holistic way of collaborating with factories and driving change in the supply chain. Moving forward, enhancements to the electricity sensors offering whether to reduce the upfront cost, or by bundling the sensors with other supplier capabilities are recommended to improve project viability.
Description
Thesis: M.B.A., Massachusetts Institute of Technology, Sloan School of Management, 2019, In conjunction with the Leaders for Global Operations Program at MIT Thesis: S.M., Massachusetts Institute of Technology, Department of Mechanical Engineering, 2019, In conjunction with the Leaders for Global Operations Program at MIT Cataloged from PDF version of thesis. Includes bibliographical references (pages 53-54).
Date issued
20192019
Department
Sloan School of Management; Massachusetts Institute of Technology. Department of Mechanical Engineering; Leaders for Global Operations ProgramPublisher
Massachusetts Institute of Technology
Keywords
Sloan School of Management., Mechanical Engineering., Leaders for Global Operations Program.