Fabrication process and electromechanical characterization of a sliding connector system for modular stretchable electronics
Author(s)
Nandy, Ananya.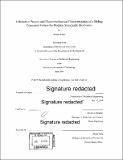
Download1130229527-MIT.pdf (8.178Mb)
Other Contributors
Massachusetts Institute of Technology. Department of Mechanical Engineering.
Advisor
Joseph A. Paradiso.
Terms of use
Metadata
Show full item recordAbstract
The development of stretchable electronics has opened the potential for novel types of wearable electronic devices that can conform to curvilinear surfaces. In the traditional wearable space, modularity has been explored as a way to make devices customizable and multi-functional. Extending modularity and customizability to stretchable electronics could allow improved data collection in contexts where traditional sensor deployment is more challenging, such as on the human body. However, the use of soft materials for creating the stretchable electronic circuits necessitates a solution to modular connections for which traditional rigid electrical connectors are not adequately suited. To address the electrical connection problem, a process was developed for fabricating a new custom connector that was intended to be integrated more easily into the stretchable electronic circuit. The sliding custom connector was evaluated against integrating off-the-shelf electrical connectors into the stretchable substrate. It was found that the custom connector had several desirable traits in comparison to the existing connectors, including a low profile, good form factor at the band interface, and easier integration into a stretchable substrate. In addition, the connector was able to achieve an average of 12.1% strain before failure, higher than the maximum 8.7% strain achieved by the snap-button, a tested off-the-shelf connector. However, the custom connector resistance was much higher, on the order of 10 [Omega] in comparison to between 0.2 and 2 [Omega] in the tested off-the-shelf connector systems. It will be necessary to pursue further iterations to reach the electrical properties afforded by the tested off-the-shelf connectors and to increase the strain before failure.
Description
Thesis: S.B., Massachusetts Institute of Technology, Department of Mechanical Engineering, 2019 Cataloged from PDF version of thesis. Includes bibliographical references (pages 48-49).
Date issued
2019Department
Massachusetts Institute of Technology. Department of Mechanical EngineeringPublisher
Massachusetts Institute of Technology
Keywords
Mechanical Engineering.