Using discrete-event simulation to increase system capacity : a case study of an assembly plant
Author(s)
Diallo, Fatima(Fatima Zahraye)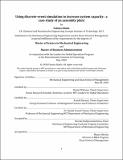
Download1191622832-MIT.pdf (1.897Mb)
Other Contributors
Sloan School of Management.
Massachusetts Institute of Technology. Department of Mechanical Engineering.
Leaders for Global Operations Program.
Advisor
Daniel Whitney, Arnold Barnett and Kamal Youcef-Toumi.
Terms of use
Metadata
Show full item recordAbstract
As part of its effort to introduce new technology and to improve the manufacturing system for the 777X production line, Boeing has made a significant capital investment in the Composite Wing Center (CWC). The new facility uses highly automated equipment and processes to support the production of components for the 777X. Since many of the automated machines are unique to the Boeing production system, opportunities exist to model and simulate specific machine systems to ensure that work is being performed as efficiently as possible. To date, most of the factory's process equipment has been installed and is operational, providing a production rate of X parts per month. To meet demand, operations will be gradually ramping up to meet the 777X production targets. The ramp-up to the target production rates will be done by a combination of additional equipment installation and process improvement projects. This research study involves the use of Discrete event simulation to provide insight into current cell capability and to identify process bottlenecks. Moreover, the simulation model incorporates process variability, the sequence of process steps within the cell, equipment downtime data, and resource constraints. The resulting simulation model was verified by comparing it to actual system performance. The model analysis and improvement recommendations show significant improvement over the current process in terms of cycle time reduction and production rates increase. In the future, the developed model will be updated regularly and will be used as a tool to monitor system throughput and to evaluate the impact of process changes to the overall system. In addition, the developed framework will be used to help other plants in a similar situation.
Description
Thesis: M.B.A., Massachusetts Institute of Technology, Sloan School of Management, in conjunction with the Leaders for Global Operations Program at MIT, May, 2020 Thesis: S.M., Massachusetts Institute of Technology, Department of Mechanical Engineering, in conjunction with the Leaders for Global Operations Program at MIT, May, 2020 Cataloged from the official PDF of thesis. Includes bibliographical references (pages 63-64).
Date issued
2020Department
Sloan School of Management; Massachusetts Institute of Technology. Department of Mechanical Engineering; Leaders for Global Operations ProgramPublisher
Massachusetts Institute of Technology
Keywords
Sloan School of Management., Mechanical Engineering., Leaders for Global Operations Program.