Six-Axis Levitated Stage with a Novel Flux-Steering Magnetic Hub Actuator
Author(s)
Anthis III, Austin Forrest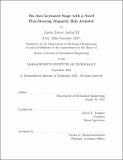
DownloadThesis PDF (79.39Mb)
Advisor
Trumper, David L.
Terms of use
Metadata
Show full item recordAbstract
This thesis presents a two-axis, permanent-magnet-biased, flux-steering actuator and its integration into a levitated stage. The hub actuator consists of a steel stator ring (165 mm OD) and a steel mover cylinder (52 mm OD). The stator has four teeth evenly spaced and pointing radially inward, each with a coil of 454 turns of AWG 20 copper wire. The teeth each have a nominal air gap of 0.5 mm with the mover, though only half of the air gap is used for motion (250 µm radius circle of travel). To increase the force density, permanent magnets are arranged to create north poles on the mover and south poles on each stator tooth to introduce a bias flux in the air gap. The coils then modulate the flux in each air gap and this difference produces a force on the mover. The hub actuator produces 200 N of force in both the X and Y directions using less than 10 W of power. In addition to the 0.5 mm stroke in the horizontal plane, we required relatively large strokes in Z and θz – 3 mm and 6∘ respectively – and designed the hub to produce approximately constant force through the range.
The six-degree-of-freedom (6 DoF) experimental stage consists of six Lorentz actuators acting on an aluminum disc stage in addition to the hub actuator. Six individual single-input, single-output (SISO) controllers stabilize and control each of the six degrees of freedom. Each coil is powered by a custom, linear, transconductance amplifier with 5 kHz bandwidth. Using the stage, we demonstrated control loop bandwidths of greater than 100 Hz for the hub degrees of freedom and RMS position noise below 0.4 µm in translation and 7 µrad in rotation. During levitated operation, we produced up to 90 N of steady state force with less than 2 W of power as well as 2.8 m/s2 acceleration in a sinusoidal position trajectory with under 2 W power dissipation. The stage was designed as an efficient fine-motion stage for photolithography or other precision positioning applications.
Date issued
2021-09Department
Massachusetts Institute of Technology. Department of Mechanical EngineeringPublisher
Massachusetts Institute of Technology