Ultrafast Laser Micromachining for Correction of Thin Optics for Next Generation X-ray Space Telescopes
Author(s)
Zuo, Heng E.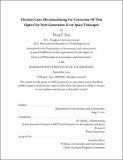
DownloadThesis PDF old (35.88Mb)
Advisor
Schattenburg, Mark L.
Terms of use
Metadata
Show full item recordAbstract
The central theme of this thesis is the development of implementing ultrafast laser micromachining technology to the correction of thin-shell lightweight high-resolution mirrors for future high performance X-ray space telescopes. The existing fabrication methods cannot achieve the required accuracy for individual mirror segments, and the high reflective coatings could distort the mirror figures beyond acceptable tolerance. As mirrors become thinner and more pliant, the need for precise and high throughput figuring methods of thin mirrors becomes more imminent.
The main contributions of this thesis is the development of two unique approaches to implement ultrafast laser micromachining technology with stress-based figure correction technique to correct for figure errors and coating distortions in thin mirrors. Rapid developments of ultrafast laser technologies have enabled high accuracy laser material processing and structuring on micron scales. By using simple optical setups with scanning X-Y stages, I showed that both equibiaxial and general biaxial stress fields can be generated with laser micromachined features in thin mirrors. The influences of various micromachining parameters have been examined to establish the effectiveness of the approach. A multi-pass correction scheme is proposed and demonstrated, where a feedback loop is implemented to induce controlled bending and reduce figure errors repeatedly. In addition, a finite element model is built to simulate the bending and stresses in thin mirrors using the stressed film patterning method with ultrafast laser micromachining, and has achieved comparable results with the experiments. Further, the breaking strengths of the mirrors treated with ultrafast laser micromachining have been evaluated, which demonstrates the proposed approaches as viable methods for processing optics for space applications.
Date issued
2021-09Department
Massachusetts Institute of Technology. Department of Aeronautics and AstronauticsPublisher
Massachusetts Institute of Technology