Solid-State Flow Control for Ion Electrospray Propulsion
Author(s)
MacArthur, Jonathan V.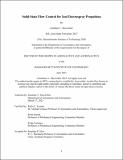
DownloadThesis PDF (100.7Mb)
Advisor
Lozano, Paulo C.
Terms of use
Metadata
Show full item recordAbstract
Electrospray propulsion offers high-efficiency, low-mass propulsive capabilities, based on ion extraction from ionic liquid propellants, to small spacecraft that exceed the capabilities of conventional chemical propulsion. Two shortcomings of such propulsion systems is their lack of lightweight propellant management due to the restrictive sizing and weight criteria for small spacecraft and the lack of a truly homogeneous porous emitter material. Lacking fluid control in these thrusters can lead to excess propellant delivery to the surface of the thruster emitter, flooding and potentially shorting the entire thruster. Use of mechanical valves and flow regulators outweigh the benefits of having such a small electric thruster in the first place. Previous work on an electrowetting valve provided a single-use activation barrier to prevent propellant from flooding the thruster's emitter prior to launch and shorting the thruster entirely. The next reasonable evolution in this propellant management area is to attain fully active control of the ionic liquid propellant in a manner analogous to conventional mechanical valves in pressurized systems. Open microfluidics are microfluidics where one surface of the liquid is unconstrained at all times. Electrowetting provides the ability to manipulate liquid wetting characteristics actively with the application of an electric potential. Combining the transport of liquids via capillary flow in open microchannels with the ability to manipulate liquid contact angle via electrowetting, a solid-state electrostatic liquid flow controller may be designed and built.
This thesis aims to tackle three primary contributions seen as improving on the aforementioned shortcomings. First, the analysis of performance envelopes for an electrowetting flow control device. Second, design, fabrication, and testing of the devices to compare with model predictions. Third, creating a new emitter material to couple with the flow controller in order to mitigate uncontrolled flow to the emitter tips. This research will shed light on the many variables at play in achieving active flow control in electrowetting open microfluidics. These analyses will grant insight into designing and fabricating micro-devices to be tested in the lab in order to verify the models. A new porous emitter material will aim to address issues with emitter uniformity that are seen in current materials, also lending to mitigation of tip flooding. A solid-state propellant management device may be coupled with future electrospray thrusters based on this thesis research.
Date issued
2023-06Department
Massachusetts Institute of Technology. Department of Aeronautics and AstronauticsPublisher
Massachusetts Institute of Technology