An Investigation of Polymer Support Structures In Metal Directed Energy Deposition
Author(s)
Kurfess, Rebecca Ann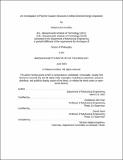
DownloadThesis PDF (17.57Mb)
Advisor
Hart, Anastasios John
Terms of use
Metadata
Show full item recordAbstract
Metal directed energy deposition (DED) can create complex components and has a high deposition rate compared to other metal additive manufacturing (AM) processes. As a result, DED is of interest to die and mold, energy, and aerospace industries, among others. However, the design space of DED is limited: overhangs steeper than 20° and freestanding bridge geometries are typically difficult or impossible to manufacture without support structures. The difficulty of support deposition and removal in DED necessitates that DED manufacturing of large components is restricted to geometries that do not require supports. The use of a dissimilar material, such as a polymer, as a support would enable lower cost, easily removable supports. The suitability of polymers as substrates in DED has not been explored due to two key unknowns: (1) the effect of the metal DED process on a polymer substrate and (2) the effect of a polymer substrate on the deposited metal. This research investigates the viability of polymers as supports in laser blown-powder DED, providing guidelines for polymer selection and print strategy to avoid detrimental polymer degradation, unsafe combustion conditions, and negative impacts of using a dissimilar substrate on the deposited metal DED component.
An understanding of combustion in the polymer/DED interaction due to laser interactions with the polymer was developed, and a tradeoff between polymer degradation and metal deposition quality was discovered. For successful DED deposition to occur, the polymer must have a high absorptivity: the polymers that facilitated deposition of 316L stainless steel in this research had absorbances greater than 2 absorbance units. Polymers with high temperature fillers, such as glass fibers or carbon fibers, were shown to be effective in mitigating the extreme thermal conditions experienced by the polymer during deposition. Degradation of polymers was measured in a series of single-bead experiments, and a series of thermal models was developed to show the influence of DED parameters and polymer material properties on the penetration of heat into the polymer substrate. Both the experimental measurements and thermal model predictions indicated degradation on the order of 1mm, an acceptable level of degradation. An understanding of the effect of a polymer substrate (CF ABS) on the hardness, microstructure, and porosity of a deposited metal (316L stainless steel) was established. Porosity of the metal was observed due the entrapment of gas from polymer degradation in the molten deposited metal. Carbon from the polymer migrated into the molten metal, causing carbide formation and increasing the hardness of the deposited metal by approximately 70% compared to the expected value. To mitigate these effects, specimens were fabricated with an interlayer cooling time, lowering the overall temperature of the deposited component and decreasing the time spent by the component at higher temperatures. The mitigation strategy was proven to reduce hardness to the expected level for 316L stainless steel manufactured with DED. Additionally, the introduction of an interlayer cooling time prevented much of the gas due to polymer degradation from infiltrating the metal component, reducing porosity from gas entrapment and cutting overall porosity from 8% to 4%.
The above findings were integrated to produce a bridge component using a polymer support structure. Overall, this research provided a methodology for selecting polymer materials, print parameters, and print strategies to enable the deposition of 316L stainless steel on CF ABS, laying the foundation for polymer support structures in metal DED.
Date issued
2023-06Department
Massachusetts Institute of Technology. Department of Mechanical EngineeringPublisher
Massachusetts Institute of Technology