Development and Application of Elastohydrodynamic Lubrication Model for Piston Pin
Author(s)
Shu, Zhiyuan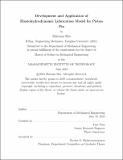
DownloadThesis PDF (15.37Mb)
Advisor
Tian, Tian
Terms of use
Metadata
Show full item recordAbstract
The piston pin, as the connection between the piston and the connecting rod, is a
crucial component in the internal combustion engine. It transfers the cylinder pressure
of combustion to the crankshaft and is subjected to high stress and harsh lubrication
conditions. Pin seizure is a severe problem in new engine development and coatings
could be a solution to this problem. However, by advancing the knowledge about the
lubrication effect and the contact patterns on the pin’s surface, it is possible to find
more cost-effective methods, such as modifying the profile or adding oil grooves.
A numerical model was developed in this study to investigate the lubrication and
dynamics of the piston pin, taking into account the deformation of the structures and
oil cavitation. The model employs multi-body dynamics and elasto-hydrodynamic
lubrication. A routine for generating and processing compliance matrices was created
and improved. Additionally, a simple built-in run-in model was utilized to modify
the pin bore and small end’s profile based on asperity contact pressure. In order to
adapt to various oil supply situations, a method for controlling the boundary oil flow
on the piston pin’s surface was also implemented.
The model was then applied to a large bore gas engine to simulate the piston pin’s
rotation and frictional forces under different operating conditions. The simulation
results indicate that hydrodynamic lubrication plays a dominant role in supporting
the normal load after break-in, and the direction and angular speed of the piston pin’s
rotation are closely linked to the operating conditions. The experimental results were
compared to the simulation, revealing the model’s reliability and accuracy.
The second part of the thesis examines the oil supply boundary conditions at the
boundaries of the lubrication areas. A computational fluid dynamics (CFD) model
was established to analyze the flow of lubricating oil at the vicinity of the pin joints,
which reveals that the amount of lubricating oil supplied from different locations can
vary. It was found that during high-speed reciprocating motion, lubricating oil may
not be able to remain on the piston pin’s surface long enough, particularly at top and
bottom. Lubricating oil flow, contact and friction patterns with different oil supply
conditions were analyzed and compared in a heavy-duty diesel engine model.
Date issued
2023-06Department
Massachusetts Institute of Technology. Department of Mechanical EngineeringPublisher
Massachusetts Institute of Technology