Local and global numerical analysis of a porous screen in free-stream flow
Author(s)
May-Varas, Nicholas A.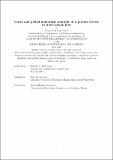
DownloadThesis PDF (16.26Mb)
Advisor
van Rees, Wim M.
Terms of use
Metadata
Show full item recordAbstract
A porous screen in a free-stream flow poses a model system for the analysis of nets, as used in fishing and aquaculture. In such applications, the forces on the net inform operational design and safety choices, whereas the flow past the net relates to the mixing of flow and nutrients in the wake. Most existing analyses of the flow past porous screens are based on experiments or simplified potential flow models. While both methods can lead to insightful results, open questions related to the details of the flow field, viscous effects, and the accuracy of the simplified models remain. To address these questions, we set up and run high-fidelity numerical simulations of the free-stream flow past a two-dimensional model porous screen. The screen is formed by placing a series of solid circular cylinders orthogonal to a free-stream flow. As the number of cylinders is increased, the gaps between them decreases, which increases the solidity of the screen. The use of a free-space domain removes any artificial numerical blockage effects, consistent with a free-stream flow.
Our analysis provides insights in the variation of the mean force coefficients as a function of the screen solidity, as well as their temporal fluctuations and spatial distributions across the screen. Further, we compute the flow rates and mean velocities through the screen gaps, and visualize the local flow field and wake. The results show that the mean value and fluctuations of the drag coefficients increase with the screen solidity. Further, the flow rate through the screen decreases monotonically as the solidity increases. The mean velocity through the screen behaves non-monotonically however, as it first increases and then decreases with screen solidity. Comparing our results to an existing potential model shows that the model predicts the flow rate well. However, the total drag coefficient is significantly lower in the predictions compared to the simulation results, pointing to the need for a better understanding of the pressure jump across the screen.
Date issued
2024-05Department
Massachusetts Institute of Technology. Department of Mechanical EngineeringPublisher
Massachusetts Institute of Technology