FrED Manufacturing - A Study in Affordable Manufacturing to Scale using Desktop Sized Fiber Extrusion Device
Author(s)
Rosko, Rachael S.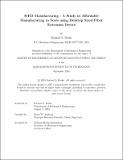
DownloadThesis PDF (29.25Mb)
Advisor
Anthony, Brian W.
Terms of use
Metadata
Show full item recordAbstract
FrED (Fiber Extrusion Device) Factory is a manufacturing facility at MIT which educates its students on fundamental and advanced manufacturing principals. The factory produces multiple FrED devices, which are "desktop fiber extrusion systems that mimic continuous fiber draw process for hands-on learning and/or laboratory experience on data acquisition, control system, and smart manufacturing. It allows learners to perform experiments, vary manufacturing parameters and control system, collect data, and perform analysis." [1] This year’s thesis work builds off of the progress from 2023, which aimed to produce a low cost variant of earlier versions of the FrED. In 2024, the aim for the lab was to implement design refinements, design for manufacturing, design the assembly line, design packaging, develop supply chain using Tulip, develop educational content, perform user testing, and execute pilot runs. The focus of this thesis will be on design refinements related to graphical user interface (GUI), inclusion of threading for improvement to program speed, and characterization of performance related to diameter control as well as advancements in educational content development, user testing, production level assembly, and pilot runs. The results of this thesis include significant improvements made to the FrED device such as a user-controlled GUI as well as close-loop controls. Furthermore, key components of the device were quantified such as fps rate of the USB camera and motor stability which aided in understanding how diameter control and modulation can be implemented in future work. At the time of submission, there were inherent complications still not understood about the FrED that limited its potential as an end user product. Some complications included reliability of the diameter reading from the USB camera, physics of the hot glue preform, and motor speed assumptions which did not perform well under close-loop testing (spool speed going to 0 in order to make the diameter larger consequently prevents the camera from reading any future diameter measurements which is problematic). In terms of pilot runs, user testing, and educational content development, the results were promising. 78.3% of the 23 user testing respondents at Venture Cafe said they were interested in receiving a FrED and getting access to more learning content. Suggestions were made by the users for future work and implementation. Educational content was developed for mass flow and data acquisition, however, a formal pilot run session where this could be tested for feedback was not performed.
Date issued
2024-09Department
Massachusetts Institute of Technology. Department of Mechanical EngineeringPublisher
Massachusetts Institute of Technology