Heat Pipes for the Thermal Management of High Frequency Transformers in the Navy integrated Power Electronics Building Block
Author(s)
Hernandez, David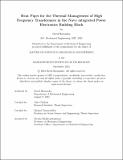
DownloadThesis PDF (19.75Mb)
Advisor
Chalfant, Julie
Triantafyllou, Michael
Terms of use
Metadata
Show full item recordAbstract
The development of the integrated Power Electronics Building Block (iPEBB) is key to the full electrification of future United States Navy ships. The creation of this modular, universal power converter takes full advantage of modern electronics; however, the high heat generation of these components, 9.6 kW from the MOSFET switches and 624 W from the transformer, makes thermal management crucial to their successful implementation. As a result of additional requirements, indirect liquid cooling using a detached cold plate is being studied; however, preliminary analysis revealed concerns regarding the hot spot temperatures of the transformer using this approach. This thesis explored the feasibility of using heat pipes to supplement the cooling provided by the cold plate to maintain iPEBB transformer core and coil temperatures below 100°C and 155°C respectively. First, experiments and analytical solutions were used to provide accurate estimates for the thermal conductivity values of the 3F36 ferrite and litz wire in the transformer. Then, a standalone thermal model of the transformer was built in StarCCM+ and used to test various cooling solutions, including forced airflow and heat pipe configurations. The proposed design utilized 16 copper-water heat pipes configured to provide alternative paths of heat flow for the regions of the transformer furthest from the cold plate. Shapal HiM Soft Machinable AlN ceramic was utilized to provide high voltage insulation, and electromagnetic simulations were used to estimate the induced losses in the heat pipes as a result of high frequency coil operations. Using a half-iPEBB thermal model, the final configuration, coupled with the cold plate cooled by 22°C deionized water at a flow rate of 0.37 kg/s, achieved a core maximum temperature of 99.7°C, coil maximum of 93.2°C, and MOSFET maximum of 144.6°C, all within their respective limits, while only adding a net weight of 0.29 kg to the iPEBB. The thermal results of this study showcase the effectiveness of heat pipes in the iPEBB and invite further analysis and experimentation to validate the electromagnetic implications of the concept. These results also contribute to the general ongoing study of heat pipe usage near high-frequency electronics.
Date issued
2024-09Department
Massachusetts Institute of Technology. Department of Mechanical EngineeringPublisher
Massachusetts Institute of Technology