Computational-Experimental Process Development for Laser Powder Bed Fusion Additive Manufacturing
Author(s)
Weißbach, Reimar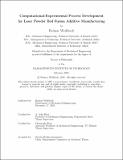
DownloadThesis PDF (94.03Mb)
Advisor
Hart, A. John
Meier, Christoph
Terms of use
Metadata
Show full item recordAbstract
Laser powder bed fusion (LPBF) additive manufacturing (AM) is instrumental for advances in high-value industries such as aerospace and medical devices. However, widespread adoption is still held back, in part due to challenges with powder handling, identification of process parameters, part qualification and quality control, and low build rates that lead to high part costs. This thesis presents workflows, tools, and understanding for practitioners and researchers seeking to address these challenges, in particular (i) powder spreading, (ii) parameter selection, and (iii) build rate improvement. Cohesive powders (D50 ≤ 20 𝜇𝑚) are challenging to spread and therefore not commonly used in LPBF, but promise more stable melting conditions during laser melting and potentially allow for finer geometrical resolution. Various spreading strategies are explored using an integrated discrete element-finite element (DEM-FEM) framework and a schematic process window for counter-rotational roller spreading is proposed. A new strategy of spreading with a transversely oscillating tool is chosen for experimental implementation and validated using a custom-built mechanized powder spreading testbed. Powder layers are analyzed using X-ray transmission imaging and layer quality is statistically correlated to kinematic spreading parameters. A methodology for performing melt track experiments using high-precision metal templates as well as a machine learning-based automated image analysis tool is presented and applied to melt track scaling studies. Based on single track parameter studies with layer thicknesses and laser spot sizes of up to 600 𝜇𝑚, a dimensionless LPBF process window using the normalized enthalpy Δ𝐻 / ℎₛ as well as the Fourier number is developed. A workflow for rapid LPBF build parameter selection is proposed, that is shown to fabricate near-full dense parts (up to 99.99 %) on the first attempt. Build rate scaling analysis reveals the trade-off between laser spot size and laser scan speed given laser power limitations. Further, LPBF with a standard powder (15 − 45 𝜇𝑚) is compared to a fine powder (0 − 25 𝜇𝑚) under similar processing conditions. The fine powder exhibits superior melt track stability and continuity, as well as significantly increased melt track cross-sectional area, allowing build rate to be increased by almost 20 %. Finally, to enable better understanding of the underlying thermo-fluid dynamics of the melt pool, an approach for computational model parameter estimation using Bayesian inference is presented and applied to the important model parameter of laser absorptivity. This is within the context of a Smooth Particle Hydrodynamics (SPH) computational melt pool model, developed collaboratively by researchers at the Technical University of Munich. The diffuse interface approach employed in SPH is validated using a discretization refinement study, showing the sensitivity of physical phenomena characteristic for LPBF, such as the vapor-induced recoil pressure, to computational hyper-parameters. These combined contributions enhance both practical implementation and theoretical understanding of LPBF, ultimately advancing the field of additive manufacturing towards more cost-effective and higher quality LPBF processes.
Date issued
2025-02Department
Massachusetts Institute of Technology. Department of Mechanical EngineeringPublisher
Massachusetts Institute of Technology