Order of magnitude scaling of complex engineering problems, and its application to high productivity arc welding
Author(s)
Mendez, Patricio F. (Patricio Fernando)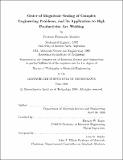
DownloadFull printable version (3.738Mb)
Other Contributors
Massachusetts Institute of Technology. Dept. of Materials Science and Engineering.
Advisor
Thomas W. Eagar.
Terms of use
Metadata
Show full item recordAbstract
This thesis presents the Order of Magnitude Scaling methodology and uses it to determine the configuration and dominant forces in the weld pool during high productivity arc welding. This methodology was developed to consistently address problems for which experimental and mathematical treatment is difficult, yet the governing equations and some general characteristics are known. The results generated by this methodology can be grouped into two sets. One of these consists of estimations of the unknowns of the problem in the form of power laws. The other is a set of dimensionless groups that indicates the relative importance of the driving forces. It is not necessary to solve the original differential equations, because they are transformed into a significantly simpler set of algebraic equations. This transformation is possible through the combination of dimensional analysis and asymptotic considerations. A new condition is introduced for normalization: that the dimensionless functions vary smoothly. This essential condition was not considered in previous research. Matrix algebra is used to provide a systematic treatment for problems involving many parameters. The application of this technique to high productivity arc welding determined for the first time that the dominant force acting on a very depressed weld pool is the arc drag force. Experimental work in 304 stainless steel was performed to analyze the effect of the large depression on defect formation. It was found that higher welding speeds (20% or more) are possible with lower sulfur content (6 ppm vs. 230 ppm). Differences in the size and stability of the weld pool depression are proposed here as the explanation for this difference. Steels with lower sulfur content show a weld pool geometry that tends to decrease the size of the gouging region (the most depressed part of the weld pool). In higher sulfur steels, the gouging region tends to extend beyond the hot region of the arc. In this situation the gouging region freezes prematurely and defects such as humping or a split bead are generated.
Description
Thesis (Ph.D.)--Massachusetts Institute of Technology, Dept. of Materials Science and Engineering, 1999. Includes bibliographical references (leaves 187-195). This electronic version was submitted by the student author. The certified thesis is available in the Institute Archives and Special Collections.
Date issued
1999Department
Massachusetts Institute of Technology. Department of Materials Science and EngineeringPublisher
Massachusetts Institute of Technology
Keywords
Materials Science and Engineering.