Pipe circularity reformation via line heating
Author(s)
Andrade, Rodrigo V. (Rodrigo Victor), 1968-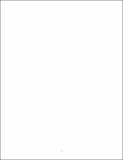
DownloadFull printable version (869.0Kb)
Other Contributors
Massachusetts Institute of Technology. Dept. of Mechanical Engineering.
Advisor
Nicholas M. Patrikalakis and Takashi Maekawa.
Terms of use
Metadata
Show full item recordAbstract
Fabrication of pipes requires the use of several manufacturing processes, such as bending, welding, drilling and wringing. However, in most cases the circular ends deviate from true circles and need reformation to be welded to angles. Currently the reformation is conducted by hammering and relies on the intuition of skilled workers. This reforming process is not only expensive but also generates unhealthy loud noise. The objective of this research is to develop an automatic system of circularizing the ends of a deformed pipe by laser line heating. The overall problem is defined as follows: Given the design of a metal pipe, measure the shape of the cross sections of both ends and a branch end of the manufactured pipe and determine the heating paths together with the heating conditions to reform the manufactured pipe to within acceptable tolerances with respect to the designed pipe using the line heating method. The line heating conditions to be applied to the pipe have to be determined in real time to make the process ecient. A Neural Network is created for this purpose and the database used to run it is generated using a simplified thermo-mechanical model of the pipe validated by a Finite Element Model (FEM).
Description
Thesis (S.M.)--Massachusetts Institute of Technology, Dept. of Ocean Engineering; and, (S.M.)--Massachusetts Institute of Technology, Dept. of Mechanical Engineering, 2001. Includes bibliographical references (leaves 119-120). This electronic version was submitted by the student author. The certified thesis is available in the Institute Archives and Special Collections.
Date issued
2001Department
Massachusetts Institute of Technology. Department of Mechanical Engineering; Massachusetts Institute of Technology. Department of Ocean EngineeringPublisher
Massachusetts Institute of Technology
Keywords
Ocean Engineering., Mechanical Engineering.