Design, analysis and optimization of the power conversion system for the Modular Pebble Bed Reactor System
Author(s)
Wang, Chunyun, 1968-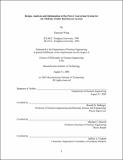
DownloadFull printable version (4.011Mb)
Alternative title
Power conversion system for the MPBR
Advisor
Ronald G. Ballinger.
Terms of use
Metadata
Show full item recordAbstract
The Modular Pebble Bed Reactor system (MPBR) requires a gas turbine cycle (Brayton cycle) as the power conversion system for it to achieve economic competitiveness as a GenIV nuclear system. The availability of controllable helium turbomachinery and compact heat exchangers are thus the critical enabling technology for the gas turbine cycle. The development of an initial reference design for an indirect helium cycle has been accomplished with the overriding constraint that this design could be built with existing technology and complies with all current codes and standards. Using the initial reference design, limiting features were identified. Finally, an optimized reference design was developed by identifying key advances in the technology that could reasonably be expected to be achieved with limited R&D. This final reference design is an indirect, intercooled and recuperated cycle consisting of a three-shaft arrangement for the turbomachinery system. A critical part of the design process involved the interaction between individual component design and overall plant performance. The helium cycle overall efficiency is significantly influenced by performance of individual components. Changes in the design of one component, a turbine for example, often required changes in other components. To allow for the optimization of the overall design with these interdependencies, a detailed steady state and transient control model was developed. The use of the steady state and transient models as a part of an iterative design process represents the key contribution of this work. A dynamic model, MPBRSim, has been developed. (cont.) The model integrates the reactor core and the power conversion system simultaneously. Physical parameters such as the heat exchangers' weights and practical performance maps such as the turbine characteristics and compressor characteristics are incorporated into the model. The individual component models as well as the fully integrated model of the power conversion system have been verified with an industry-standard general thermal-fluid code Flownet. With respect to the dynamic model, bypass valve control and inventory control have been used as the primary control methods for the power conversion system. By performing simulation using the dynamic model with the designed control scheme, the combination of bypass and inventory control was optimized to assure system stability within design temperature and pressure limits. Bypass control allows for rapid control system response while inventory control allows for ultimate steady state operation at part power very near the optimum operating point for the system. Load transients simulations show that the indirect, three-shaft arrangement gas turbine power conversion system is stable and controllable. For the indirect cycle the intermediate heat exchanger (IHX) is the interface between the reactor and the turbomachinery systems. As a part of the design effort the IHX was identified as the key component in the system. Two technologies, printed circuit and compact plate-fin, were investigated that have the promise of meeting the design requirements for the system ...
Description
Thesis (Ph. D.)--Massachusetts Institute of Technology, Dept. of Nuclear Engineering, 2003. Includes bibliographical references. This electronic version was submitted by the student author. The certified thesis is available in the Institute Archives and Special Collections.
Date issued
2003Department
Massachusetts Institute of Technology. Department of Nuclear Engineering; Massachusetts Institute of Technology. Department of Nuclear Science and EngineeringPublisher
Massachusetts Institute of Technology
Keywords
Nuclear Engineering