A resorbable polymeric microreservoir device for controlled release drug delivery
Author(s)
Grayson, Amy Catherine Richards, 1975-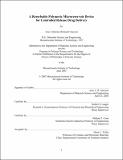
DownloadFull printable version (6.741Mb)
Other Contributors
Massachusetts Institute of Technology. Dept. of Materials Science and Engineering.
Advisor
Robert S. Langer and Michael J. Cima.
Terms of use
Metadata
Show full item recordAbstract
The method by which a drug is delivered can have a significant effect on the drug's therapeutic efficacy. Pulsatile delivery of certain drugs and molecules (such as hormones) has been shown to more efficacious than continuous delivery, as the fluctuation in concentration levels in vivo more closely mimics the natural physiological processes of the human body. However, there is a shortage of systems that are capable of delivering drugs in this manner, particularly if it is desired to have a self-contained system that does not require external stimulation to trigger device function. The objectives of this thesis were to design, fabricate, test, and characterize a biodegradable polymeric microreservoir device that is capable of delivering multiple pulses of drugs in a reproducible manner. This polymeric microreservoir device contains an array of reservoirs that are each covered by a thin membrane of a degradable polymer. Control over the release of drugs from the device was achieved by changing the molecular weight of the reservoir membranes. The current prototypes have 36 reservoirs, but the size and geometry of the polymeric chip could be designed to optimize device performance depending on the application for which it will be used. Changing the membrane materials or thicknesses could change the time at which the chemicals are released from the reservoirs. Each reservoir on the device could potentially have a different set of membrane characteristics, enabling release of the contents of each reservoir at a different time. A fabrication process for these devices was developed, that consists of two compression-molding steps, followed by microinjection of the reservoir membranes from solution and subsequent drying of the membranes under vacuum and elevated temperature. The devices are then loaded with the drugs to be released and sealed at room temperature. This fabrication process avoids exposure of the drugs to solvents and high temperatures that may adversely affect their stability. Further, the compression-molding process used to fabricate the main body of the device, as well as minimal solvent used in the fabrication of the reservoir membranes, were designed to minimize adverse effects upon in vivo implantation due to residual solvent. Poly(L-lactic acid) was selected as the component material for the device substrate, while (cont.) the reservoir membranes were made from copolymers of poly(lactic-co-glycolic acid) having varying molecular weights. The degradation behaviors of these materials have been extensively studied both in vitro and in vivo, and they have been shown to be quite biocompatible. Studies showed that the degradation of the reservoir membranes in vitro and subsequent release times of chemicals from the reservoirs is a function of both the membrane thicknesses and environmental temperature. Proof-of-principle release studies showed up to four pulses of radiolabeled molecules (¹⁴C-dextran, ³H-heparin, and ¹²⁵I-HGH) from single devices, both with one chemical per device (four pulses per chemical) as well as two chemicals per device (two pulses per chemical). Bioactivity measurements showed that heparin released from the devices in vitro retains activity up to at least 143 days ...
Description
Thesis (Ph. D.)--Massachusetts Institute of Technology, Dept. of Materials Science and Engineering, 2003. Includes bibliographical references. This electronic version was submitted by the student author. The certified thesis is available in the Institute Archives and Special Collections.
Date issued
2003Department
Massachusetts Institute of Technology. Department of Materials Science and EngineeringPublisher
Massachusetts Institute of Technology
Keywords
Materials Science and Engineering.