Experimental investigation of microfabricated bipropellant rocket engines
Author(s)
Protz, Christopher S. (Christopher Stephen), 1977-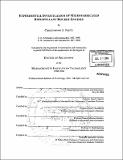
DownloadFull printable version (65.69Mb)
Other Contributors
Massachusetts Institute of Technology. Dept. of Aeronautics and Astronautics.
Advisor
Alan H. Epstein.
Terms of use
Metadata
Show full item recordAbstract
As satellite missions begin to require smaller satellites, launch systems and attitude control thrusters of reduced mass will be required. Microrocket engines could provide a low mass, high specific impulse, modular answer to these needs. These small rocket engines would produce thrust of order of 10's of Newtons at a thrust-to-weight of over 1000, over 10 times the thrust-to-weight of conventional chemical liquid bipropellant engines. The first microrocket engine thrust chamber and nozzle design measures 18 x 14 x 3 mm and is fabricated from single crystal silicon using MEMS microfabrication techniques offering the promise of low cost in production. This thesis describes an experimental investigation of bi-propellant microrocket engines and encompasses the fields of materials, microfabrication, combustion and chemical kinetics, instrumentation, packaging, and fluid dynamics. It builds on London's earlier gaseous propellant work, expanding the operating envelope of his motors to higher thrust levels and using these results to design liquid bi-propellant regeneratively cooled engines. Failure analysis of the original devices indicated failures were primarily caused by structural design flaws. Second generation gaseous propellant devices were built and tested. Providing reliable packaging interfaces between the macro test setup and the device proved very difficult. Two packaging methods involving modified geometries and glass seals were developed and allowed higher performance tests. Combustion experiments spanned a range of oxidizer-to-fuel ratios by mass of 1.6 to 2.5 and reached a maximum chamber pressure of 30 bar with a maximum thrust of 3 N at a thrust coefficient of 1.12. A maximum c* of 1650 m/s has been recorded. (cont.) Experimental results were compared with CFD predictions which suggest that the low thrust coefficient of these devices is due to the overexpansion of gases in the nozzle at the test pressures in combination with the planar extruded nozzle geometry. CFD suggests that at higher chamber pressures the thrust coefficient will approach values up to 90-95 percent of the 1-D ideal case. Experimental values of characteristic exhaust velocity are in agreement with non- adiabatic predictions indicating that combustion is nearly complete. The chamber pressure and thrust limits in the current devices are due to localized failures at bond interfaces in the coolant passages. The potential of the current design is limited to approximately 60 bar by the coolant passage pressure limit, chamber structural limit, and injector manifold pressure limit. Potential liquid propellants for a regeneratively cooled storable bipropellant microrocket engine are examined. The design space for devices using these propellants is explored based on the thermal, structural, and fabrication constraints, and a design for a regeneratively cooled microrocket engine utilizing liquid nitrogen tetroxide and liquid JP-7 as propellants at a vacuum specific impulse of 267 s is presented. Directions for improved specific impulse engines include increasing the engine size by a factor of 2 to 4 and continuing research on hydrogen peroxide as a coolant.
Description
Thesis (Ph. D.)--Massachusetts Institute of Technology, Dept. of Aeronautics and Astronautics, 2004. MIT Institute Archives copy: p. 301-328 bound in reverse order. Includes bibliographical references (p. 325-328).
Date issued
2004Department
Massachusetts Institute of Technology. Department of Aeronautics and AstronauticsPublisher
Massachusetts Institute of Technology
Keywords
Aeronautics and Astronautics.