Combustion systems for power-MEMS applications
Author(s)
Spadaccini, Christopher M. (Christopher Michael), 1974-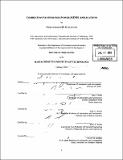
DownloadFull printable version (25.11Mb)
Alternative title
Combustion systems for power-microelectromechanical systems applications
Other Contributors
Massachusetts Institute of Technology. Dept. of Aeronautics and Astronautics.
Advisor
Ian A. Waitz.
Terms of use
Metadata
Show full item recordAbstract
As part of an effort to develop a micro-scale gas turbine engine for power generation and micro-propulsion applications, this thesis presents the design, fabrication, experimental testing, and modeling of the combustion system. Two fundamentally different combustion systems are presented; an advanced homogenous gas-phase microcombustor and a heterogeneous catalytic microcombustor. An advanced gas-phase microcombustor consisting of a primary and dilution-zone configuration is discussed and compared to a single-zone combustor arrangement. The device was micromachined from silicon using Deep Reactive Ion Etching (DRIE) and aligned fusion wafer bonding. The maximum power density achieved in the 191 mm³ device approached 1400 MW/m³ with hydrogen-air mixtures. Exit gas temperatures in excess of 1600 K and efficiencies over 90% were attained. For the same equivalence ratio and overall efficiency, the dual-zone microcombustor reached power densities nearly double that of the single zone configuration. With more practical hydrocarbon fuels such as propane and ethylene, the device performed poorly due to significantly longer reaction time-scales and inadequate fuel-air mixing achieving maximum power densities of only 150 MW/m³. Unlike large-scale combustors, the performance of the gas-phase microcombustors was more severely limited by heat transfer and chemical kinetics constraints. Using all available gas-phase microcombustor data, an empirically-based design tool was developed, important design trades identified, and recommendations for future designs presented. Surface catalysis was identified as a possible means of obtaining higher power densities with storable hydrocarbon fuels by increasing reaction rates. Microcombustors with a similar (cont.) geometry to the gas-phase devices were fitted with platinum coated foam materials of various porosity and surface area. For near stoichiometric propane-air mixtures, exit gas temperatures approaching 1100 K were achieved at mass flow rates in excess of 0.35 g/s. This corresponds to a power density of approximately 1200 MW/m³; an 8.5-fold increase over the maximum power density achieved for gas-phase propane-air combustion. Low order models including simple time-scale analyses and a one-dimensional steady-state plug flow reactor model, were developed to elucidate the underlying physics and to identify important design parameters. High power density catalytic microcombustors were found to be limited by the diffusion of fuel species to the active surface, while substrate porosity and surface area-to-volume ratio were the dominant design variables. Experiments and modeling suggest that with adequate thermal management, power densities in excess of 1500 MW/m³ and efficiencies over 90% are possible within the microengine pressure loss constraint and the material limits of the catalyst. A materials characterization study of the catalyst and its substrate revealed that metal diffusion and catalyst agglomeration were likely failure modes.
Description
Thesis (Ph. D.)--Massachusetts Institute of Technology, Dept. of Aeronautics and Astronautics, June 2004. "February 2004." Includes bibliographical references (p. 261-270).
Date issued
2004Department
Massachusetts Institute of Technology. Department of Aeronautics and AstronauticsPublisher
Massachusetts Institute of Technology
Keywords
Aeronautics and Astronautics.