Coordinating the multi-retailer, single supplier procurement processes for a seasonal product with supply contracts
Author(s)
Prisby, Craig K. (Craig Kanoa), 1971-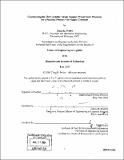
DownloadFull printable version (1.094Mb)
Other Contributors
Massachusetts Institute of Technology. Engineering Systems Division.
Advisor
James M. Masters.
Terms of use
Metadata
Show full item recordAbstract
Supply contracts are used to maximize profits in a supply chain by coordinating order quantities between the suppliers and retailers. In traditional supply contracts, retailers use a newsvendor approach to maximize their profits, while the supplier's profits increase linearly as a function of the number of units supplied to retailers. Initially, retailers assume risk in the supply chain because they are facing an unknown demand, and the suppliers assume no risk. This thesis looks at an example from the garment industry where retailers order to replenish stock after a small assortment buy is placed at the start of the finite selling season. The suppliers must place production orders for the entire selling season before the selling season begins. It is clear see that the retailers assume little risk in this model, while the supplier faces significant risk, especially if its forecasting methods are not accurate. The levels of risk that each assumes in this model are reversed when compared to the traditional supply contract model. A method is developed that coordinates the retailer ordering with the supplier's production schedule. It is shown that coordinating the supply chain's ordering will lead to higher profits than the current, uncoordinated model.
Description
Thesis (M. Eng. in Logistics)--Massachusetts Institute of Technology, Engineering Systems Division, 2003. Includes bibliographical references (p. 24).
Date issued
2003Department
Massachusetts Institute of Technology. Engineering Systems DivisionPublisher
Massachusetts Institute of Technology
Keywords
Engineering Systems Division.