Vibration and crack detection in gas turbine engine compressor blades using Eddy current sensors
Author(s)
Lackner, Matthew, 1980-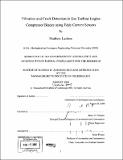
DownloadFull printable version (11.93Mb)
Other Contributors
Massachusetts Institute of Technology. Dept. of Aeronautics and Astronautics.
Advisor
James D. Paduano.
Terms of use
Metadata
Show full item recordAbstract
(cont.) in the ECS signal, no definitive method for sensing blade vibration using an ECS has yet been developed. High cycle fatigue (HCF) cracks generated by compressor blade vibrations are a common source of failure in gas turbine engines. Current methods for crack detection are costly, time consuming, and prone to errors. In-situ blade vibration detection would help operators avoid critical engine speeds, and help infer the presence of cracks via a change in the mode of a blade. Blade vibrations can be detected using non-contacting sensors like optical sensors, or contacting sensors like strain gauges. These methods have drawbacks that make them poorly suited for installation in a gas turbine engine. Eddy Current Sensors (ECS) have numerous advantages over other vibration detection methods. This thesis aims to use ECS's for vibration detection. Testing was performed in a spin pit rig in the Gas Turbine Lab at the Massachusetts Institute of Technology. The rig contained a rotor on which three test blades spun, and strain gauge and ECS data were extracted from the rig. Magnet arrays were used to provide an excitation force to the blades, causing them to vibrate as they were spinning. Force hammer testing was used to determine the resonant frequencies and mode shapes of the test blades, as well as transfer functions from the strain gauges to the blade tip acceleration. These transfer functions allowed for independent knowledge of the blade vibration behavior. The case of a cracked blade was also considered. Estimates were performed to determine the proper location and length of a crack in the test blade. A 10 mm edge crack was created in a test blade. The crack was found to lower the resonant frequency of the first torsion mode of the blade by 0.2%, and to alter the transfer function between strain and tip acceleration. While some evidence of the blade vibration appears
Description
Thesis (S.M.)--Massachusetts Institute of Technology, Dept. of Aeronautics and Astronautics, September 2004. Includes bibliographical references (p. 97).
Date issued
2004Department
Massachusetts Institute of Technology. Department of Aeronautics and AstronauticsPublisher
Massachusetts Institute of Technology
Keywords
Aeronautics and Astronautics.