A framework for designing interlayers for ceramic-to-metal joints
Author(s)
Park, Jin-Woo, 1972-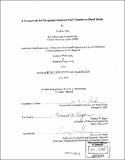
DownloadFull printable version (6.100Mb)
Other Contributors
Massachusetts Institute of Technology. Dept. of Materials Science and Engineering.
Advisor
Thomas W. Eagar.
Terms of use
Metadata
Show full item recordAbstract
Engineering ceramics have become widely used as structural materials due to their excellent mechanical and thermal properties at high temperature. In most structural applications, ceramics are integrated as critical components in a system that is largely metallic and have to be joined frequently to metals. During joining processes, residual stresses are induced in the joints due to the large differences in physical properties between ceramics and metals, which degrades the mechanical integrity of the joints. This thesis proposes improved design rules for interlayers used to accommodate residual stresses in ceramic-to-metal joints. Efforts have been made on developing theoretical understanding of the important factors affecting residual stresses. Using Finite Element Method (FEM) simulations and Order of Magnitude Scaling (OMS), our understanding could be summarized and generalized as closed-form analytical equations. In these equations, the accumulated elastic strain energy in the ceramic has been used as a more reliable metric for quantifying residual stresses and predicting failure stress. The equations provide a useful functional relationship between the strain energy, material properties, and joint geometry. To the best of our knowledge, they are the first analytical expressions explaining the plasticity effect in the ceramic-to-metal joints. In these equations, the strain energy normalized by the scaling factor consisting of dominant parameters is a linear function of dimensionless groups of secondary important parameters. The physical implication of each dimensionless group also has been clearly defined. Based on analytical equations, improved interlayer design rules have been proposed and verified experimentally. (cont.) Among the dimensionless groups, 4), the ratio of CTE difference between the interlayer and each base material, represents the stress distribution in the interlayer and its effect on plastic deformation in the interlayer. With smaller cD, the stress distribution between two interfaces becomes uniform and symmetric resulting in larger plastic deformation of the interlayer, which accommodates more strain energy. This parameter indicates that although the CTE of an interlayer cannot be modified in practice, the use of additional interlayers can redistribute the residual stresses in the interlayer and exploit the ductility of the interlayer more efficiently. Based on this fact, use of rigid layers with increasing CTE away from the ceramic interface and insertion of ductile layers between each rigid layer is proposed as a better multiple interlayer design than multiple interlayers with graded CTE. In the equations, strain energy increases proportional to the joint radius cubed. Controlled porosities have been incorporated in the interlayer by patterning to reduce the joint area, hence to decrease the strain energy. Shear test results confirmed our design rules for multiple and patterned interlayers. For patterened interlayers, an optimized level of porosity in the interlayer without interface weakening could be found. Although the effects of all the parameters cannot be considered, experimental results confirmed that our understanding addresses dominant parameters for joint strength with simple equations that provide a useful viewpoint in designing ceramic-to-metal joints ...
Description
Thesis (Ph.D.)--Massachusetts Institute of Technology, Dept. of Materials Science and Engineering, 2002. Includes bibliographical references (p. 163-168).
Date issued
2002Department
Massachusetts Institute of Technology. Department of Materials Science and EngineeringPublisher
Massachusetts Institute of Technology
Keywords
Materials Science and Engineering.