Forecasting manufacturing variation using historical process capability data : applications for random assembly, selective assembly, and serial processing
Author(s)
Kern, Daniel C. (Daniel Clifton), 1974-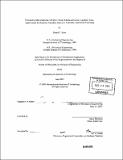
DownloadFull printable version (36.77Mb)
Other Contributors
Massachusetts Institute of Technology. Dept. of Mechanical Engineering.
Advisor
Anna Thornton.
Terms of use
Metadata
Show full item recordAbstract
In today's competitive marketplace, companies are under increased pressure to produce products that have a low cost and high quality. Product cost and quality are influenced by many factors. One factor that strongly influences both is manufacturing variation. Manufacturing variation is the range of values that a product's dimensions assume. Variation exists because no production process is perfect. Often times, controlling this variation is attempted during production when substantial effort and resources, e.g., time, money, and manpower, are required. The effort and resources could be reduced if the manufacturing variation could be forecast and managed during the design of the product. Traditionally, several barriers have been present that make forecasting and managing variation during the design process very challenging. The first barrier is the effort required of a design engineer to know the company's process capability, which makes it difficult to specify tolerances that can be manufactured reliably. The second barrier is the difficulty associated with understanding how a single manufacturing process or series of processes affects the variation of a product. This barrier impedes the analysis of tradeoffs among processes, the quantifying of the impact incoming stock variation has on final product variation, and the identification of sources of variation within the production system. The third barrier is understanding how selective assembly influences the final variation of a product, which results in selective assembly not being utilized efficiently. In this thesis, tools and methods to overcome the aforementioned barriers are presented. A process capability database is developed to connect engineers to manufacturing data to assist with (cont.) detailing a design. A theory is introduced that models a production process with two math functions, which are constructed using process capability data. These two math functions are used to build closed-form equations that calculate the mean and standard deviation of parts exiting a process. The equations are used to analyze tradeoffs among processes, to compute the impact incoming variation has on output, and to identify sources of variation. Finally, closed-form equations are created that compute the variation of a product resulting from a selective assembly operation. Using these tools, forecasting and managing manufacturing variation is possible for a wide variety of products and production systems.
Description
Thesis (Ph. D.)--Massachusetts Institute of Technology, Dept. of Mechanical Engineering, 2003. Includes bibliographical references (p. 337-340).
Date issued
2003Department
Massachusetts Institute of Technology. Department of Mechanical EngineeringPublisher
Massachusetts Institute of Technology
Keywords
Mechanical Engineering.