Elastically averaged precision alignment
Author(s)
Willoughby, Patrick (Patrick John), 1978-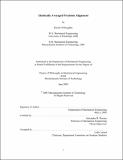
DownloadFull printable version (24.52Mb)
Other Contributors
Massachusetts Institute of Technology. Dept. of Mechanical Engineering.
Advisor
Alexander H. Slocum.
Terms of use
Metadata
Show full item recordAbstract
One of the most important steps in designing a machine is the consideration of the effect of interfaces between components. A badly designed interface can vary from costly difficulties such as additional control or calibration to machine failure. For precision assemblies such as automobile engines, robotics, and many measurement devices, exact constraint techniques have been used to align removable components. Exact constraint typically requires controlled precision machining to allow an interface to be repeatable and interchangeable. Elastic averaging techniques can be used instead of exact constraint to create less repeatable interfaces with more generous machining requirements. Elastic averaging represents a subset of coupling types where improved accuracy is derived from the averaging of errors over a large number of relatively compliant contacting members. Repeatability and accuracy obtained through elastic averaging can be nearly as high as in deterministic systems, elastic averaging design allows for higher stiffness and lower local stress when compared to kinematic couplings. In this thesis, a model of elastic averaging has been developed to predict the effects of manufacturing variations on design. To demonstrate the capabilities of this model, a new fiber optic connector has been designed with elastic averaging and precision injection molding in mind. Simulations predict repeatability of approximately 5 micrometers for a 5X scale version, which agreed with experimental measurements. Fidelity parts were produced using the Silicon Insert Molded Plastics process (SIMP). SIMP uses microfabricated silicon inserts in a traditional injection mold to create parts with micro-scale features. (cont.) The SIMP fidelity parts were measured to estimate manufacturing repeatability of approximately 5 micrometers. Using this repeatability, simulations predict that the actual scale version has repeatability of approximately 0.5 micrometers
Description
Thesis (Ph. D.)--Massachusetts Institute of Technology, Dept. of Mechanical Engineering, 2005. This electronic version was submitted by the student author. The certified thesis is available in the Institute Archives and Special Collections. Includes bibliographical references (p. 107-110).
Date issued
2005Department
Massachusetts Institute of Technology. Department of Mechanical EngineeringPublisher
Massachusetts Institute of Technology
Keywords
Mechanical Engineering.