Design of a fast cycle time hot micro-embossing machine
Author(s)
Dirckx, Matthew E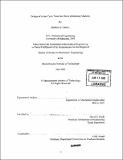
DownloadFull printable version (14.75Mb)
Alternative title
Fast cycle time HME machine
Other Contributors
Massachusetts Institute of Technology. Dept. of Mechanical Engineering.
Advisor
David E. Hardt.
Terms of use
Metadata
Show full item recordAbstract
In the coming years, there will be a huge market for mass-produced polymer micro- devices. These devices include microfluidic "labs on a chip," micro-optical chips, and many others. Several techniques exist for producing micron-scale features in polymer materials. One of the most promising of these techniques is Hot Micro-Embossing (HME). In this process, a thermoplastic polymer workpiece is heated above its glass transition temperature and a micro-patterned die is forced into it. The polymer conforms to the workpiece and the features are replicated. Much of the research to date concerning HME has not addressed fundamental issues that will be central to successful mass production using this process. There is a compelling need to study HME from the perspective of manufacturing process control. In order to conduct such a program, a HME machine is needed that allows the operator to precisely control all the potentially significant process parameters. No existing machine fully meets this requirement. This thesis concerns the conceptual and detailed design of a HME system, including the platen assembly and the temperature control system. A parametric model and finite element analysis were used to guide the design of the platen assembly and to assess its thermal and structural performance. A dynamic thermal model of the temperature control system was developed. This model was used to guide the selection of components and to predict the performance of the system as a whole. The new design will have a short cycle time, will permit the use of full wafer-size embossing tools, and will be able to follow a user- programmed trajectory in displacement, force, and temperature.
Description
Thesis (S.M.)--Massachusetts Institute of Technology, Dept. of Mechanical Engineering, June 2005. "June 2005." Includes bibliographical references (leaves 163-165).
Date issued
2005Department
Massachusetts Institute of Technology. Department of Mechanical EngineeringPublisher
Massachusetts Institute of Technology
Keywords
Mechanical Engineering.