Prioritization and integration of lean initiatives with theory of constraints
Author(s)
Schwain, Kevin D. (Kevin Douglas), 1974-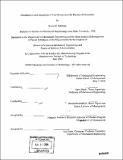
DownloadFull printable version (3.657Mb)
Other Contributors
Leaders for Manufacturing Program.
Advisor
Dave Hardt and Donald Rosenfield.
Terms of use
Metadata
Show full item recordAbstract
The principles of lean manufacturing have taken hold in a number of manufacturing firms as a means of achieving operational excellence through continuous improvement. Womack and Jones have suggested a generalized process for lean transformation in their 1996 book, Lean Thinking. A key element of this process is the creation of value stream maps for each product line. Value stream maps are the basis for planning and tracking a firm's lean transformation. Rother and Shook go further in their 1998 work Learning to See as they describe how these maps are created and then integrated into both the transformation process and the regular business planning cycle. The authors note that difficult questions remain, including: "In what order should we implement?" and "Where do we start?" Advice offered by Rother and Shook is helpful but insufficient given the complexity of many business environments and the scarcity of resources in competitive industries. This thesis builds upon Rother and Shook's work in proposing a framework for prioritizing lean initiatives. Specifically, Theory of Constraints (TOC) tools are employed as a basis for selecting programs and projects that provide the greatest system-wide productivity improvement for the least cost. In this manner, application of the proposed prioritization framework results in a more effective and efficient lean transformation. Research at the Eastman Kodak Company illustrates how this framework can be applied in a paper finishing production facility. Results highlight the system constraint in the paper slitting operation and the high leverage of machine changeover time in productivity improvement. We conclude that the Theory of Constraints can provide an effective focusing tool for the lean enterprise.
Description
Thesis (M.B.A.)--Massachusetts Institute of Technology, Sloan School of Management; and, (S.M.)--Massachusetts Institute of Technology, Dept. of Mechanical Engineering; in conjunction with the Leaders for Manufacturing Program at MIT, 2004. Includes bibliographical references (leaves 44-45).
Date issued
2004Department
Leaders for Manufacturing Program at MIT; Massachusetts Institute of Technology. Department of Mechanical Engineering; Sloan School of ManagementPublisher
Massachusetts Institute of Technology
Keywords
Sloan School of Management., Mechanical Engineering., Leaders for Manufacturing Program.