Centralization of manufacturing processes at a major automotive OEM
Author(s)
Kornick, Adam Marcus, 1974-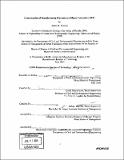
DownloadFull printable version (2.738Mb)
Other Contributors
Leaders for Manufacturing Program.
Advisor
David Simchi-Levi and Thomas Roemer.
Terms of use
Metadata
Show full item recordAbstract
Ford is moving from decentralized control of manufacturing processes to centralized control. Prior to this centralization effort, product development occurred as a central function, but individual plants were largely allowed to select vendors, machine tools, suppliers, etc. for production without central oversight (other than accounting and cost control). Ford has now formed a group, manufacturing engineering, within powertrain operations (PTO), as well as analogous groups in other business units, to standardize and centralize these functions for the production of engines and transmissions. To date, the group has formally centralized machine design and purchasing with some success and a fair amount of upheaval in the daily tasks of on- site launch team members. Two technical aspects of this shift are examined, beginning with higher communication costs. These costs are the time and effort spent relaying information to understand and select a course of action for a production network rather than a course of action for a single plant. Communication costs for Ford are shown to increase with the number of plants or platforms involved in a product or process decision. After evaluating these delays, methods to improve communication costs by modifying individual responsibilities as well as methods used by other centralized manufacturers are discussed. In addition to modifying communication across the production network, common production processes also allow for flexible production within the network. Once plants share common equipment and processes they can produce the same products. A simple model is used to demonstrate that the network becomes more flexible and opportunities arise to improve the overall supply chain for engine production. (cont.) The first order effects of this flexibility are shown to be increased utilization and fewer stockouts. However, second order effects of production scheduling and inventory management problems arise because the broader supply chain has not yet been modified to incorporate plant floor flexibility. Suggested improvements to address these second order effects are also discussed.
Description
Thesis (M.B.A.)--Massachusetts Institute of Technology, Sloan School of Management; and, (S.M.)--Massachusetts Institute of Technology, Dept. of Civil and Environmental Engineering; in conjunction with the Leaders for Manufacturing Program at MIT, 2004. Includes bibliographical references (p. 74-75).
Date issued
2004Department
Leaders for Manufacturing Program at MIT; Massachusetts Institute of Technology. Department of Civil and Environmental Engineering; Sloan School of ManagementPublisher
Massachusetts Institute of Technology
Keywords
Sloan School of Management., Civil and Environmental Engineering., Leaders for Manufacturing Program.