Reducing variability in a semiconductor manufacturing environment
Author(s)
Penttilä, Minja Johanna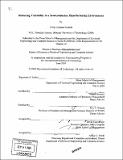
DownloadFull printable version (8.444Mb)
Other Contributors
Leaders for Manufacturing Program.
Advisor
Thomas Roemer and Roy E. Welsch.
Terms of use
Metadata
Show full item recordAbstract
The main drivers in today's flash memory business are low cost and flexibility. Low cost requires high tool utilizations, whereas flexibility and ability to respond quickly to changing customer demands require short throughput times. There is, however, an inherent operational conflict with achieving both high utilization and short cycle time simultaneously. Intel's flash memory factory is striving for shorter manufacturing throughput times without reducing tool utilizations. One of the major components in throughput time today is queuing time caused partly by variability in the manufacturing environment. Being able to reduce this variability component could result in improvements in throughput time. In this work, Factory Physics methods are used to analyze variability in the manufacturing flow. First, potential high variability areas in the flow are identified. Second, manufacturing data is analyzed to find the main sources of variability. Third, ways to reduce variability are investigated. Finally, means to align manufacturing metrics with variability reduction efforts and the effect of metrics on organizational culture and change implementation are discussed. During the study it was found out that the lithography area reduces the overall manufacturing flow variability. It was also found out, that the area is highly utilized and is thus introducing non-value adding queuing time for the product throughput time. (cont.) Arriving material flow was identified to be the main source of variability. Recommendations for improving the area performance include optimizing tool dedications, standardizing operator decision making, and changing preventive maintenance operations. The key takeaway from this study is the importance of metrics alignment. Metrics are the most powerful incentives for operator behavior. Unless the daily floor level performance measurements are aligned to support the organizational goals, implementing new operations management methods to reduce variability will be challenging.
Description
Thesis (M.B.A.)--Massachusetts Institute of Technology, Sloan School of Management; and, (S.M.)--Massachusetts Institute of Technology, Dept. of Electrical Engineering and Computer Science; in conjunction with the Leaders for Manufacturing Program at MIT, 2005. Includes bibliographical references.
Date issued
2005Department
Leaders for Manufacturing Program at MIT; Massachusetts Institute of Technology. Department of Electrical Engineering and Computer Science; Sloan School of ManagementPublisher
Massachusetts Institute of Technology
Keywords
Sloan School of Management., Electrical Engineering and Computer Science., Leaders for Manufacturing Program.