Application of a design optimization strategy to multi-stage compressor matching
Author(s)
Bert, Jérôme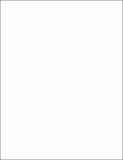
DownloadFull printable version (16.16Mb)
Other Contributors
Massachusetts Institute of Technology. Dept. of Aeronautics and Astronautics.
Advisor
Zoltán S. Spakovszky.
Terms of use
Metadata
Show full item recordAbstract
A major challenge in the design of multi-stage compressors is the matching of stages to enable stable operation over a large range of mass flows and operating conditions. Particularly in turbofan low-pressure compressors, where a variable geometry cannot be implemented, design strategies for maximum efficiency at high speed can compromise the surge margin at low speed. In this thesis, a design optimization framework has been implemented to an industry-strength compressor-matching problem. The optimization framework combines a mean-line flow solver and a dynamic stability analysis of a six-stage low-pressure compressor of a modern turbofan engine to optimize the blade row geometry for enhanced stability at flight idle conditions. To assess the potential improvements in compressor stability at low speed, a number of optimization strategies are employed using different objective functions and stability metrics. To estimate the performance and stability of the six-stage compressor, a mean-line flow solver is developed and coupled with a previously developed dynamic compressor-stability analysis. A fan-root flow model and an endwall loss correlation are developed using performance data provided by industry. (cont.) The analysis reveals that the models enable an adequate estimation of the datum compressor performance. This methodology is then used in an optimization effort searching for the optimum compressor design. A compressor blade parametrization based on Bezier splines is developed to explore a range of possible blade geometries. A CFD-based blade-row performance database is established using the blade-to-blade solver MISES. This facilitates an effective means to predict the blade performance for various geometries defined by the optimizer. To find the best solution for the compressor-matching problem, a number of optimization strategies are applied to the datum compressor. The best result is obtained using an optimization strategy based on industry surge margin. An improvement of 14.8% in flight idle surge margin is achieved while maintaining the design pressure ratio and efficiency at climb speed within 1% and 0.3 points of the design values respectively. A compressor design optimization based on a dynamic-stability metric is also employed. Due to time constraints, this strategy could not be fully explored and the preliminary results suggest that further work is required. (cont.) The best results is a 14.8% improvement in the flight idle surge margin, but the re-matching of the compressor and the associated increase in the rotor loading of the second stage entail high-risk design modifications. This suggests that, given these design limitations, the best matching is achieved by the datum configuration. In summary, the thesis demonstrates that the developed compressor design optimization methodology is applicable to industry-strength design problems, and the framework is shown to have the potential to investigate compressor designs for optimum matching.
Description
Thesis (S.M.)--Massachusetts Institute of Technology, Dept. of Aeronautics and Astronautics, 2006. Includes bibliographical references (p. 96-97).
Date issued
2006Department
Massachusetts Institute of Technology. Department of Aeronautics and AstronauticsPublisher
Massachusetts Institute of Technology
Keywords
Aeronautics and Astronautics.