Design, fabrication, and testing of a three-dimensional monolithic compliant six-axis nanopositioner
Author(s)
Labuz, James (James R.)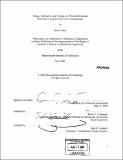
DownloadFull printable version (2.669Mb)
Other Contributors
Massachusetts Institute of Technology. Dept. of Mechanical Engineering.
Advisor
Martin L. Culpepper.
Terms of use
Metadata
Show full item recordAbstract
The purpose of this research was to demonstrate the feasibility for creating a three-dimensional monolithic compliant six-axis nanopositioner. Much of this work was based off of the original two-dimensional HexFlex manipulator created by Prof. Martin Culpepper and a three-dimensional design by Samuel Korb. The compliant mechanism was manufactured from a single sheet of 1/8 inch 5052 Aluminum. The mechanism was designed to be fabricated on the non-precision, abrasive water-jet and to be formed using bending processes. The fabrication process was successful. The entire machining process was on the order of one hour. The forming process was repeated multiple times without failure of the mechanism in all cases. The formed mechanism was tested to characterize its ability to manipulate the positioning stage both in- and out-of-plane. The transmission ratio for in-plane was measured at 6.4 while the out out-of-plane ratio was 6.3. The input deflection vs. output deflection curves display a linear relationship, but there was .0003 inches of hysteresis seen in the out-of-plane data after a max deflection of .0009 inches. This amount of hysteresis is undesirable and leaves further testing to determine its causes.
Description
Thesis (S.B.)--Massachusetts Institute of Technology, Dept. of Mechanical Engineering, 2006. Includes bibliographical references (leaf 36).
Date issued
2006Department
Massachusetts Institute of Technology. Department of Mechanical EngineeringPublisher
Massachusetts Institute of Technology
Keywords
Mechanical Engineering.