The role of lean manufacturing principles and strategic alternatives in achieving business goals
Author(s)
Ramaswamy, Dhananjay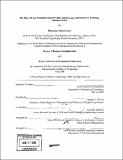
DownloadFull printable version (9.037Mb)
Other Contributors
Leaders for Manufacturing Program.
Advisor
Stephen C. Graves and Daniel E. Whitney.
Terms of use
Metadata
Show full item recordAbstract
Lean Manufacturing is widely accepted as a proven method to achieve operational excellence. Many manufacturers undertake lean manufacturing implementations as a strategy to improve competitiveness and realize business objectives. However, despite the wealth of literature on the success of lean manufacturing, it should not be viewed as a panacea for every business situation. A key challenge is to estimate the true benefits that a lean implementation is likely to provide, and compare them to the requirements of the business. This thesis provides a framework for such an analysis in the context of the Detroit Forge facility of American Axle & Manufacturing, Inc (AAM). AAM has been facing some significant challenges in the recent past, including skyrocketing steel prices, the prospect of declining sales and contractually fixed labour costs. AAM has launched a corporate wide lean manufacturing initiative to eliminate waste from its plants, and to make them more competitive. The actual improvement achievable at each plant will vary depending upon the current state of the plant, the nature of the operations and type of equipment used. (cont.) If the expected improvements do not satisfy the business requirements, options beyond the realm of pure operations must be considered, and are referred to as strategic alternatives. The analysis begins by characterising the current state and developing a vision of the future state using the tool of value stream mapping. We develop a model that predicts necessary supermarket buffers, changeovers and working hours as well as the associated costs, based upon fundamental process and plant parameters. The model is applied to the current and future states to predict the financial improvements that could be achieved by the lean initiative, based on the current cost structure of the operation. Finally we propose a framework for developing and analysing possible strategic alternatives to achieve the business goals. A wide range of alternatives was considered, including technology development, labour agreement renegotiation, outsourcing and optimisation of plant loading. This project resulted in the implementation of a pull scheduling system in axle shaft manufacturing, as well as input to the revitalisation efforts at Detroit Forge.
Description
Thesis (M.B.A.)--Massachusetts Institute of Technology, Sloan School of Management; and, (S.M.)--Massachusetts Institute of Technology, Dept. of Mechanical Engineering; in conjunction with the Leaders for Manufacturing Program at MIT, 2006. Includes bibliographical references (p. 105-106).
Date issued
2006Department
Leaders for Manufacturing Program at MIT; Massachusetts Institute of Technology. Department of Mechanical Engineering; Sloan School of ManagementPublisher
Massachusetts Institute of Technology
Keywords
Sloan School of Management., Mechanical Engineering., Leaders for Manufacturing Program.