Implementing lean material management in an extended value stream
Author(s)
Harper, Justin A., 1975-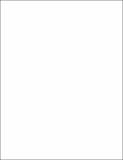
DownloadFull printable version (8.504Mb)
Other Contributors
Leaders for Manufacturing Program.
Advisor
Stanley Gershwin and John Carroll.
Terms of use
Metadata
Show full item recordAbstract
American Axle & Manufacturing, Inc. (AAM) is still in the process of transitioning to a culture of "lean manufacturing" as opposed to the current culture of "mass production". This thesis involved working with AAM employees and suppliers at various locations to understand how material flows between and within AAM's plants, the reasons for and analysis of the current state of material management, and opportunities for improvement. Attention is also given to the cultural and business context in which this work takes place, and the issues relating to efforts to implement change in large industrial organizations. This work produced two strategic-level products and one tactical-level product to improve lean material management at AAM described herein. Cultural observations are also provided. At the strategic level, one project focused upon making extended value stream maps of material flow between AAM plants and suppliers/processors. This information allows all decision-makers at AAM to objectively examine a common set of information, information which was previously unavailable to any one individual. Extended value stream mapping allowed supply chain inventory and lead time-reduction opportunities to be identified. (cont.) The focus upon extended value streams increased awareness of the need to more fully account for costs in making part procurement decisions. Therefore, a second strategic project involved the development of a total cost decision tool, and its use in making sourcing decisions. This computer spreadsheet-based tool uses simple inputs to quickly produce a more all-encompassing estimate of the total costs of purchasing parts from a given supplier. Traditionally, only piece-price plus freight costs were used to determine sources of supply. Other, additional factors may alter the decision of which supplier to use if they are considered. The tactical-level project involved implementation of a lean pull system. This project involved coordinating teams at two separate axle shaft manufacturing plants to implement a more effective visual pull system between and within the plants, using lean concepts for material management and flow. A final aspect of the thesis was to examine the current business context in which the lean systems are to operate, as well as the strategic, cultural, and political aspects that influence change management in large organizations. (cont.) One conclusion drawn from the internship is that the firm should start emphasizing visual control on the plant floor, and less supervisor work on paper in their offices after their shifts end. If the production boards and visual controls are in constant disarray, this needs to be resolved as quickly as a failed customer delivery, because it is fundamentally undercutting the ability of the organization to improve what it provides to customers through better quality and productivity. It also hinders efforts to reduce costs to bid for new work. Failing to attract new work is as damaging as a failed customer delivery, except that it will happen a year from now rather than today.
Description
Thesis (S.M.)--Massachusetts Institute of Technology, Dept. of Mechanical Engineering; and, (M.B.A.)--Massachusetts Institute of Technology, Sloan School of Management; in conjunction with the Leaders for Manufacturing Program at MIT, 2007. Includes bibliographical references (p. 99-101).
Date issued
2007Department
Leaders for Manufacturing Program at MIT; Massachusetts Institute of Technology. Department of Mechanical Engineering; Sloan School of ManagementPublisher
Massachusetts Institute of Technology
Keywords
Mechanical Engineering., Sloan School of Management., Leaders for Manufacturing Program.