Carbon nanotube based electromechanical probes
Author(s)
Yaglioglu, Onnik, 1976-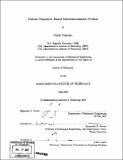
DownloadFull printable version (23.76Mb)
Other Contributors
Massachusetts Institute of Technology. Dept. of Mechanical Engineering.
Advisor
Alexander H. Slocum.
Terms of use
Metadata
Show full item recordAbstract
Electromechanical probing applications continuously require smaller pitches, faster manufacturing and lower electrical resistance. Conventional techniques, such as MEMS based cantilever probes have their shortcomings in terms of the lowest pitch that can be achieved, cost and yield. Given their promising mechanical and electrical properties, carbon nanotubes (CNTs) are strong candidates for future probing applications. A new class of metal-CNT hybrid electromechanical probes is presented where vertically aligned carbon nanotube structures, grown with a chemical vapor deposition (CVD) technique, act as elastic springs, and a metal coating on the probes is used for increased electrical conduction. This design and architecture presents a scalable approach where thousands of probes can be fabricated in very short production times. 1.5 Ohm resistance and reliable performance for 6000 cycles at 50 [mu]m over-travel was achieved for a column of 200 [mu]m x 200[mu]m cross-section and 1plm of Au deposition. In-situ scanning electron microscope mechanical compression tests revealed a unique deformation mechanism of the CNT structures where continued compression results in successive buckle formation which later can serve as micro-bellows and elastic springs. (cont.) A novel stiffness tuning method is presented to control the elastic properties of a given CNT probe by controlling the initial compressing amount. Further stiffness tuning is achieved by changing gas composition during CVD growth where CNT diameter and density is modified. Lateral compression and densification tests show that these CNT structures are highly anisotropic and have very different deformation mechanisms in vertical and lateral directions. Mechanical properties resulting from two main CVD growth techniques, namely fixed catalyst where a thin film of catalyst layer is deposited onto the growth substrate, and floating catalyst where the catalyst particles are introduced in the gas phase, are compared. It is found that floating catalyst CVD growth yields much stiffer structures due to the relatively larger CNT diameters. As the adhesion of CNT structures to the growth substrate is very weak and the support layer is typically an insulator, a versatile transfer printing technique is developed which enables simultaneous placement and reinforcement of the probes on a wide range of substrates, including metals and printed circuit boards. Electromechanical performance and failure mechanisms of fully functional metal-CNT hybrid probes are presented.
Description
Thesis (Ph. D.)--Massachusetts Institute of Technology, Dept. of Mechanical Engineering, 2007. Includes bibliographical references (p. 131-137).
Date issued
2007Department
Massachusetts Institute of Technology. Department of Mechanical EngineeringPublisher
Massachusetts Institute of Technology
Keywords
Mechanical Engineering.